Barton Marine celebrating 75 years
by Barton Marine 21 Jul 2023 04:46 AEST
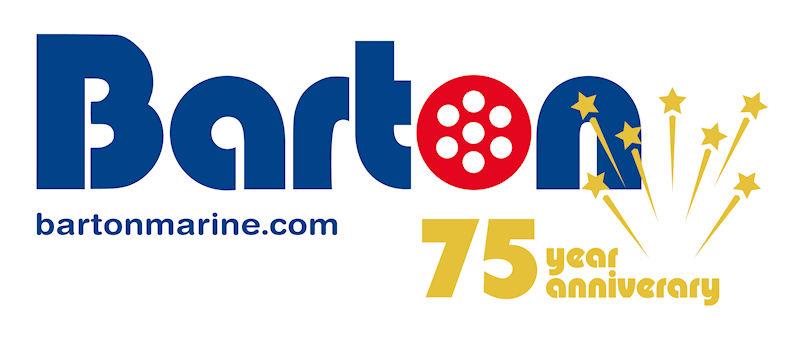
75 Years Anniversary © Barton Marine
2023 sees Barton Marine celebrating 75 years as a successful British manufacturer of hardware for the marine and general industrial sectors. This is a compelling story, played out over the last seven and a half decades, with the principal mission and ideals of supplying highest quality engineered product that provide confidence and value to sailors and industrial customers.
Barton's production strategy reveals a well-thought-out model to supply one-stop shopping for high performance design, manufacturing, assembly and despatch, allowing Barton to supply their customers with marine and industrial equipment in a rapid timeframe. The Barton brand is distributed in 35 countries and territories with a stand-alone company in the US, Barton US LLC, and the Barton Team continues to embrace the traditional values the company is known for, providing superior customer service for their product ranges worldwide.
When engaging with Barton's staff, what is most evident is their pride in their British-made products. Chatting with Jeff Webber, the Chief Commercial Officer, he offered a real insight into Barton's approach to stock management. Rather than just storing large quantities of finished carded equipment on shelves, they instead maintain a substantial inventory of raw materials and components. This enables them to respond swiftly to customer orders, making the right product at the right time. Jeff compared this process to building with Lego blocks - having the necessary components readily available allows them to assemble large orders of various deck equipment for rapid despatch. With over 1000 products in the catalogue, stock control is a careful balancing act, so Barton maintains a running inventory of most products, in the range, for immediate despatch. Having a UK based factory and administrative office provides the advantage of oversite and continuity of quality in manufacturing and allows for immediate despatch.
Suzanne Blaustone, CEO of Barton Marine, took us on a tour of their facility located in Whitstable, Kent. We began on the upper floor, where the administration and sales teams work in large, open-plan offices, creating a relaxed and friendly environment. Arriving early, we had the opportunity to attend the daily production meeting, led by Dermot Bealey, Production Director. As Dermot worked through the current schedule, it became evident how their operational model functioned. By 9.30am, a large number of products required for client despatch had already moved from component stock to assembly or were enroute to despatch.
Descending to the factory floor, we met Joyce, Piece Parts Supervisor, who has worked for Barton for many years and whose main role is component inventory control and picking. With her extensive experience at the company, she knows the components required for each product and meticulously handpicks them from bins, placing them in production trays ready for the assembly team. The computer system generates work orders and picking lists whenever there is insufficient pre-made stock, or when stock levels fell below predetermined levels. Speaking with Joyce, we learn that her role not only entails providing the assembly team with the correct number of components but she is also responsible for conducting quality control checks at this stage.
The assembly department next door is supervised by Dave, who has a team of people working with him during normal production periods, although there is capability to expand during times of high demand. It is a smooth process with the trays prepared by Joyce ready for technical assembly the moment the previous batch is on its way to packaging and QC. It is lovely to see that Barton's people show a wide range of ages on the floor, all who seem connected both by a love and appreciation of sailing and a pride in the manufacturing process, from teen sailor Harry Newton who joined Barton as their 'Rising Star' as an up-and-coming laser sailor, to Dave who sails a 40' racing trimaran as part of a team.
The care and attention given to quality control is impressive, as each deck hardware component is inspected before it goes into final assembly. Dave emphasised the importance of this practice and showed us an example where they detected an assembly issue affecting the aesthetics of a product. Although the original unit as is, would not have impacted the operational use, a slight adjustment restored the sleek look of the part. This is just one example of the pride Barton takes in their manufacturing process, always prioritising a flawless result. As Dave said, 'we won't build it, if it's not right'. It also highlights the efficiency of their in-house operations strategy, that a delay caused by product improvement while still achieving customer deadlines, is a system that works on multiple levels of continuity of quality and customer service.
Continuing our tour, we followed the production process from assembly to despatch. The despatch and storage areas serve as the final quality control checkpoint, as well as a hub for ready-to-ship products. The stores team fulfil orders by picking and packing from their stock bins or through the arrival of a stock order from the assembly department. Ed, who is responsible for this area, explained that due to Barton's huge variety of global customers, each order has varying shipping requirements, and they make every effort to accommodate these. They also use a range of courier services to ensure that their customers receive the best service in their individual countries.
Suzanne was keen to show us more of the production facility by heading back down the line to component manufacturing. One central area focuses on moulding and houses Barton's plastic injection moulding machines, which produce component parts in marine grade plastics which make up the mainstay of the Barton product range. Having been in manufacturing since 1948, Barton have a well-oiled process to meet lead times for order requirements, incorporating set up times, running times quality checks and unit counts for storage.
In the next bay is the machine shop, which boasts a wide array of machinery, including mills, lathes, metal slitters, benders and presses. Here, the team primarily work with stainless steel and aluminium components, but they also handle in-house repairs and any upgrades to the moulding tools. Dermot explained that besides their own engineering team and machines, they also have a network of local subcontractors for added support. This arrangement allows for flexibility in the supply chain, mitigating machine downtime and facilitating prompt parts procurement when needed.
Aluminium track, for track and car systems, as well as sliding roof and door systems, all extruded exclusively in the UK, is brought in-house for drilling, cutting to length, curving and bending as well as any additional order customisation, before being sent off to a specialist anodiser. Extrusion processing operates on a weekly turnaround, so track can be ready within 10 days from the date of order, even if it entails custom specifications.
We reviewed additional in-house facilities, including polishing, track bending, load testing, cycle testing, and material testing. It was impressive to witness the comprehensive range of processes and testing procedures undertaken in-house at Barton to ensure the highest standards of quality and performance.
Reflecting on our experience and summing up with Suzanne at the conclusion of our visit, she highlighted an important aspect of the company's culture. Many of the staff members are not only experienced technicians, but also sailing and boating enthusiasts. It means that Barton receives instant feedback on their products directly from those who use them, even before the items hit the shelves or reach the dealers.
The real secret to Barton's success though is the dedication and pride that the entire team take in developing and delivering the highest quality products direct from British waters.
As Suzanne commented, "Barton is always striving for continuous improvement and innovation and we are focused on delivering the products and value that sailors require to make their sailing experience even better."
This winning formula will carry on into the future to ensure that sailors and industrial customers have access to the highest quality hardware products when they need them.
Find out more at bartonmarine.com