A quick dive into a keel project
by William Souter, MarsKeel 22 Oct 2020 09:10 PDT
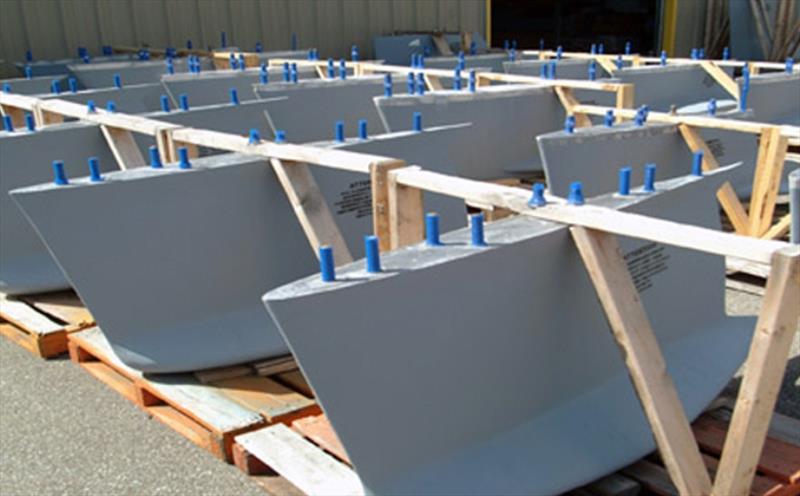
A quick dive into a keel project © MarsKeel
At MarsKeel Technology we offer our clients all the services needed to manufacture top quality keels. We are far more than a lead foundry, we offer complete project management, design, and engineering assistance.
Our support begins with the first email or phone call. We discuss the project with the customer, be it the builder, designer, or engineer. From there, we get an idea of the scope of work. Once the drawings arrive, we really get the opportunity to get into the details of the project. It is from this point that we can see exactly what the customer is looking for. Is it a "simple" lead casting? Or is it a more complete keel combining castings, fabrications, and machining?
We Can Assist You
Which type of project are you asking for? This is where our experience assists you. We can assist you through both very complex projects (left KZ7 keel) involving many disciplines, from pattern making, casting, fabrication and CNC machining to far more simple keel castings (4200 lbs keel casting)..
Costing
This going to be dull but very necessary. Once we know where in the range of projects you are, we can start creating a costing sheet. We work out a costing sheet for every job. It is not just a means of adding costs, that's simple, it reminds you to look carefully at every detail in the project. No matter if you have seen them hundreds of times or they are brand new. From a simple 15-line costing sheet to a tremendously complex 200-line costing sheet, it helps both us and the customer get what they want. They are a road map for the project.
Manufacturing and Designing
There are two basic parts to this process. One, looking at the offered design and seeing if there is any aspect that we can offer suggestions on. This is not always necessary, but we always look for areas where we can assist make the project simpler, and possibly less expensive.
The second process is the internal manufacturing engineering work that is done. This is the design and production work to make every part needed to make the project, from patterns to custom shipping systems. This can be as simple as a single bolt rack or as complex as a complete system of fabricated core boxes and machined rods. These are the things that the customer will not see but they are a tremendously important part of making the project and need to be included in the costing sheet. Without them, we couldn't do our work. It all depends on the complexity of the project how involved the manufacturing engineering needs to be.
Below are some possible areas we could offer suggestions to the designer or customer. These two are generally the simplest ways of saving the customer time and money. They of course need to be accepted by the engineer or designer. There are many other areas that we look at as well, but we don't have the space to go through all of them here.
Example 1: Fabricated Fin Material
In terms of a keel fin, be it fabricated or cast, machined partly or completely, this is where our team is likely to have suggestions for the project. Our suggestions are not being critical of the shape or geometry of the keel, they are focused on construction details. We are always looking for new ways to make things like we all are, better, cheaper, and faster. We offer the customer suggestions on things like the material required in a fabricated fin. If for example, they spec a SSAB Weldox grade, we would suggest a grade of ASTM A 514. This material has the same chemical and physical properties, it is less expensive and is available locally.
Example 2: Keel Bolts
We might suggest something as small as a change in keel bolt material to offer a less expensive option if ABS or ISO bolt calculations allow the change. We can make keel bolts or studs and hex and jam nuts out of any material that is needed, from 17-4Ph to 2205 Duplex to NAB. But some smaller projects can have the cost impacted by making custom machined keel bolts and hex nuts rather than a readily available option, 316 SS or A4-70.
Conclusions
You can now understand the services and level of detail that we offer in all our projects. It is this level of detail that is reflected in the costing sheet and in the offered price. This is not to say that we overthink the project but based on our experience try to foresee and plan paths around any found concerns. If we can be successful in that then the product and the customer will get the part they are looking for. It will arrive on-site anywhere in the world safe and sound.
That is the basis for every question we ask and every option we offer, to get the customer the best part that we can make at a reasonable price and delivery time.
Read the latest blog for an in-depth look at our complete keep project process.