North Sails- Working with Classics in an Aramid Age
by Richard Gladwell on 26 Jun 2012
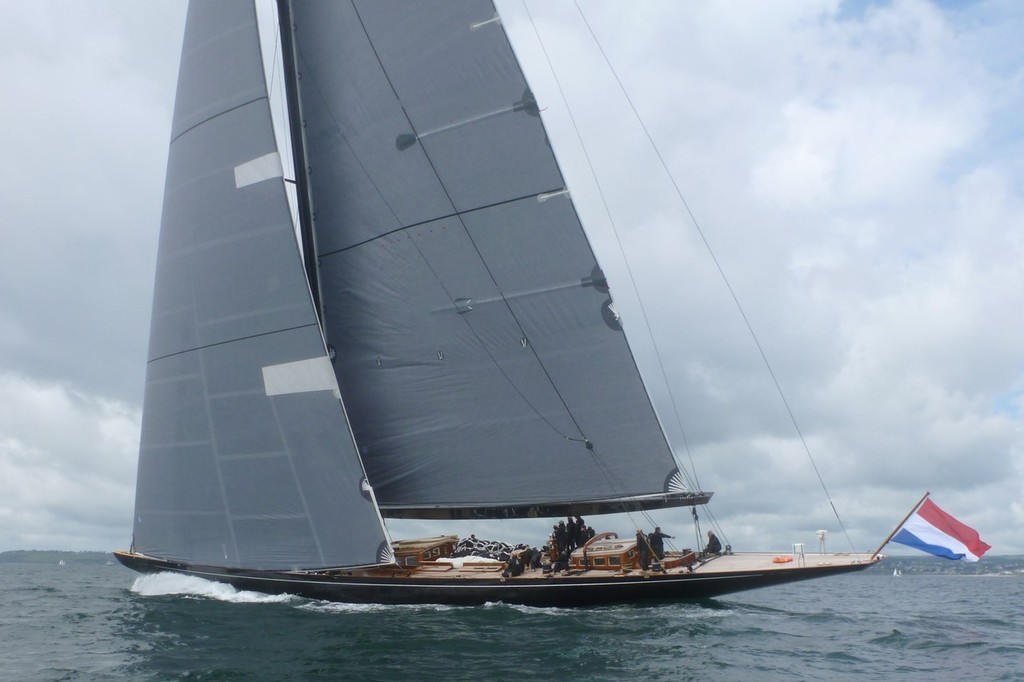
The recently restored J class, Endeavour, sailing off Falmouth with a suit of 3Di sails J Class Association
In the Aramid Age of Sailmaking, grey sails are becoming an increasing sight amongst harbour and club racers, as well as on the international racing scene.
The rapid take up of the new technology of 3Di has surprised even North Sails’ NZ Designer, Burns Fallow. 'Two years ago we would have had ten 3DL sails for every 3Di. Now it is about even.'
The distinctive grey coloured 3Di sails are being put together in North Sails Pakenham St loft - just over the way from Auckland’s Viaduct Harbour - action central for many international sailing campaigns and superyacht fit-outs.
Less obvious is the steady flow of massive J class sails out of Pakenham Street destined for the 120ft plus classics of the 1930’s but now enjoying a resurgence of racing in the traditional regatta venues in Europe and East Coast USA .
In the first half of 2012, sails have been built in Auckland for five of the octogenarian genre - Lionheart, Endeavour, Rainbow, Valsheda, and Ranger.
The size of the J-class mainsails are impressive – 500sq metres - about the size of a modern residential section. The spinnakers are double that at close to 1000sq metres, and are made in the same Pakeham Street loft. Each J class sail is individual with differences between the two being on the rig dimensions, or the type of inventory required. Some carry two overlapping jibs, others just one.
'It is like ordering a custom Ferrari and wanting it in two months time', Burns Fallow explains.
'The J class is certainly a beautiful boat but they certainly don’t rest on their laurels, and when these guys race, they do so extremely competitively. They are at the same level as the TP52’s and the likes. You have a group of owners who are successful business people. They all want to win, and they are all used to winning.'
'3Di is quite a different product from 3DL which we’ve had since the early 1990’s and started in the 1992 America’s Cup, and was then used extensively in all the America’s Cup through to 2007 and even 2010 with the soft sails that were used by Oracle and Alinghi.'
'The 3Di product was actually developed about five years ago by Alinghi, and was originally a black sail, but because of a lack of development time, they could not race with it.
'After the 2007 America’s Cup, Norths came to an agreement with Alinghi, to continue development and what we have now is the characteristic grey coloured sails that are right through most grand prix racing fleets.
Why grey sails?
The grey is in fact just a surface colour, and the sails can be any colour required. The first five Volvo boats that carry North Sails are all coloured, including Telefonica which has blue sails. Puma has black sails, as does Abu Dhabi, Groupama is green and Camper is white.
'You can have the surface any colour you like, but it is what is inside that is doing the work.'
The sails actually have a thin semi-translucent white outer layer, and the grey appearance is triggered by the combination of that outer colour and the black of the carbon inside. With 3Di sails there is no mylar or other film that is inherent in the older technologies.
'Building a 3Di sail is much more like building a boat, you have unidirectional filaments. It is much more complex structurally, consequently it has less stretch, and more of the wind’s energy is transferred into the boat.'
The 3Di sails are built as a moulded blank in the North Sails facility in Minden, Nevada and shipped to the loft for finishing and fitting.
Most of the actual process involved in the manufacture of the 3Di blank is very different from the 3DL, with the common point being the final stage where the sails are left to cure on the mould before being rolled up for shipping or air freight.
Internal construction
Like the 3DL sails the 3Di’s arrive in the North’s loft as a rolled up blank.
There the difference stops. 3Di’s construction offers a lot more options including fitting the battens inside the sail itself, rather than the traditional external attachment method. Burying the battens into the sail is both smoother on the outside, reducing drag, but allows a lot more reinforcement to be built internally into the blank in each batten area, before the whole construction is surfaced.
Although 3Di is being used extensively in the Volvo Ocean Race, with all the top five boats using 3Di the trickle down effect is well underway. Locally, NZ’s largest one design keelboat class, the Young 88, have several competitors using 3Di.
'It’s certainly getting into the mass market very quickly,' says Fallow. 'Pricewise they are 10-15% above 3DL. Not a huge step, but in my experience 3Di is easily as big a jump as 3DL was over panelled sails from the early 90’s.
The key advantage of 3Di is that it is more stable from a structural perspective.
'The layup of the tapes inside 3Di can be varied much more than with 3DL or any string sail. With string sails you have to go from one corner to another or the edge of a sail,' Fallow explains.
3Di is made up of a series of carbon tapes that are 150mm wide. This allows a specific area to be covered with the tape, according to the structural engineering requirements, and doesn’t have to go all the way to the edge of the sail – allowing its construction to be optimised.
'The key difference is that all other sails are made from yarns, which are a group of filaments which are twisted together, and they retain some spring because of their twisted nature. 3Di is made from filaments which are laminated straight onto the sail with much less crimp. When load goes on the sail the filaments take the load immediately, as there is much less spring,' he says.
3Di sails do not have to be made of carbon, in fact some classes like the Volvo 70 rules prohibit carbon. Kevlar is used as the contraction fibre, but still using the same 3Di construction method.
Thick, strong corners
The difference between the other technologies and 3Di really becomes apparent at the tack, head and clew of the sails. With 3Di this is the thickest and strongest part of the sail, the edge of the J class sail at this point, with literally hundreds of layers of filament in the sail-corner building to a piece about the thickness of a finger, and as inflexible as a board.
That thickness and stiffness soon reduces towards the centre of the sail – in fact within a metre on the J class sail, to the point where it is as thin and flexible as would be expected on a conventional sail, but of course very smooth, because all the reinforcing is carried within the sail itself, rather than being carried externally as is done on other constructions.
'The boats are getting bigger, and we used to talk about tonnes of load on a sail, now we are talking about tens of tonnes. There are 15 to 18 tonnes of load going through the corner, or focal point, of a J class sail.'
How all that load is transferred on to the boat has changed markedly as well. Gone are the massive stainless steel rings - replaced with smaller, lighter and much stronger titanium fittings.
Corner fittings are still attached with webbing, but with 3Di the webbing is only to attach the ring to the sail, not add reinforcing, or spread load. All that is all contained within the sail itself. The sewing machines Norths currently use cannot go through anything thicker than a 20mm piece of plywood. All finishing in the thicker areas of the 3Di sail has to be done in the traditional manner, going back to when sails were made of canvas – stitched by hand.
'Since the arrival of Kevlar, sails haven’t got a lot lighter. But they have got a lot more resistant to stretch. That is really what is driving the development, not the overall weight reduction. We would rather add more efficient material to reduce stretch, and keeping the same weight, than remove material at the gain of some weight, but getting an increase in stretch.
Fallow moves over to a 3DL sail blank on the same floor, pointing out that the sail is made up of hundreds of filaments, which are in a spiral and don’t lay straight. He explains that the twisted filament analogy is analogous with a piece of laid rope. 'By going to the straight filament of 3Di, we take nearly all the spring out of the system.'
Any filament laid in a 3DL sail in a high load area has to be taken all the way to the other side of the sail, while with 3Di in the reinforcing material can just be laid in the specific area without the need to start and end on the edge of the sail.
The second part of this story will be published tomorrow...
If you want to link to this article then please use this URL: www.sail-world.com/98941