Why is carbon fiber so expensive?
by Rachel Swaby on 4 Oct 2011
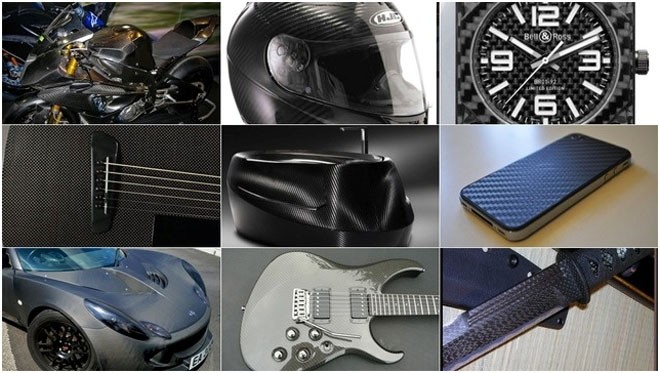
SW
When carbon fiber was first trotted out in solid rocket motor cases and tanks in the 1960s, it was poised to not only take on fiberglass, but also a whole host of other materials.
What happened?
50 years later it's still an exotic material. Sure, Batman's got it in his suit, expensive cars feature smatterings of it in their dashboards and performance parts, but at $10 a pound on the low end, it's still too pricy for wide-scale deployment. We've been using this stuff for decades. Where's our materials science Moore's Law to make this stuff cheap? Why is this stuff still so expensive?
Turns out that even half a century later, this stuff is still a major pain in the ass to make.
Before carbon fiber becomes carbon fiber, it starts as a base material—usually an organic polymer with carbon atoms binding together long strings of molecules called a polyacrylonitrile. It's a big word for a material similar to the acrylics in sweaters and carpets. But unlike floor and clothing acrylics, the kind that turns into a material stronger and lighter than steel has a heftier price tag. A three-ish-dollar per pound starting price may not sound exorbitant, but in its manufacturing, the number spikes.
See, to get the carbon part of carbon fiber, half of the starting material's acrylic needs to be kicked away. 'The final product will cost double what you started with because half burns off,' explains Bob Norris of Oak Ridge National Laboratory's polymer matrix composites group. 'Before you even account for energy and equipment, the precursor in the final product is something around $5 a pound.'
That price—$5 a pound—is also the magic number for getting carbon fiber into mainstream automotive applications. Seven bones will do, but five will make the biggest splash. So as it stands, the base material alone has already blown the budget.
There's more. Forcing the acrylic to shed its non-carbon atoms takes monstrous machines and a lot of heat. The first of two major processing steps is oxidization stabilization. Here fibers are continuously fed through 50-100 foot-long ovens pumping out heat in the several hundred degrees Celsius range. The process takes hours, so it's a massive energy eater.
Then the material goes through a what's called carbonization. Although the furnaces here are shorter and don't run for as long, they operate at much higher temperatures—we're taking around 1000 degrees Celsius for the initial step before and then another round of heating with even higher temperatures. That's a power bill you don't even want to think about.
Full story at http://gizmodo.com
If you want to link to this article then please use this URL: www.sail-world.com/89307