Composites a viable alternative to aluminium
by Rob Mundle on 4 Nov 2008
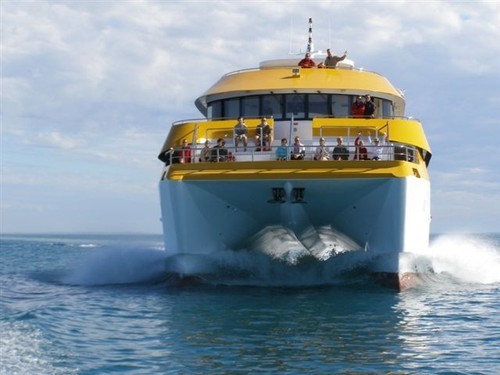
Spirit of Hervey Bay’ gets down to business SW
Composite construction has again been proven as a viable alternative to aluminium for the construction of commercial vessels with the successful sea trials, and initial commercial operation, of the 24-metre long whale watching catamaran ferry, Spirit of Hervey Bay, in Queensland, Australia.
Built using ATL Composites’ unique DuFLEX Composite Panel System, the vessel has exceeded all expectations, both in construction and operation, so much so that the designer, Noah Thompson, has had no hesitation in declaring, ‘This is the way of the future.’
‘In a world where fuel economy is now king, this boat proves that composite construction is becoming the alternative to aluminium,’ Thompson continued. ‘The combination of an efficient design, the use of ATL Composite materials and engineering services, and a superb build has led to the creation of a commercial vessel that has exceeded all expectations.’
Thompson, whose company East Cape Marine Ltd. is based in Te Puke, in New Zealand’s Bay of Plenty, is seen as a rising star in naval architecture.
This was the largest project undertaken by all concerned --- ATL Composites, the designer, and the builders, Streamline Catamarans, of Hervey Bay --– using a custom prepared DuFLEX Component Pack, and it was supremely successful. These Component Packs, which are created at ATL’s facility on Australia’s Gold Coast using state-of-the-art CNC routing machinery, have already been acclaimed throughout the boatbuilding industry for their quality and the significant savings they bring to a project, especially through a reduction in labour costs and the minimisation of waste material.
In endorsing the DuFLEX system, Noah Thompson said: ‘My personal view is that ATL Composites creates a superior boatbuilding product. With the owner requesting a high volume, light displacement vessel that would operate at speed and be very fuel efficient, we saw DuraKore composite hull planking, and DuFLEX composite panels for the topsides and superstructure, as the logical choice.
‘What has been most encouraging is that Spirit of Hervey Bay clearly shows there is no limit when it comes to the size of the Component Packs that ATL can produce. Bigger projects are now on my drawing board using DuraKore and DuFLEX routed packages.
‘Yes, there is a lot more design time involved in the creation of a complex 3D program, but this is outweighed by the fact that the Component Packages that are created from the program save a massive amount of construction time, primarily through a significant reduction in the number of man-hours. Compared to traditional boatbuilding where you so often see a major cost over-run, this ATL product proved to be exceptional with the ease of assembly. The CNC-routed pack had every component numbered, so when it arrived at the Streamline factory each piece could be easily identified and put into place in the assembly process, just like a huge Meccano set.’
Another benefit derived from DuFLEX structural panels is that the design requires fewer frames and ring frames to form the structure of the vessel when compared to a similar sized aluminium vessel. This reduction in frames and the light weight properties of the DuFLEX Panels contributes to a significant weight saving overall. This weight saving extends further because in being lighter the vessel requires smaller engines and less fuel capacity to achieve design performance targets.
The head of Streamline Catamarans, Wayne Jones, was equally enthusiastic about ATL products when it came to building the triple deck Spirit of Hervey Bay: ‘This is the largest vessel by volume that we have built, and our decision to use DuraKore and a DuFLEX Component Package made the construction much quicker and easier,’ he said. ‘It is the technology associated with these products that is revolutionising the way boats can be built lighter and stronger.’
The design specification for Spirit of Hervey Bay required a service speed of between 18 and 20 knots with 245 passengers on board. Currently she is achieving 21 knots at 1800rpm, and there is ample evidence of a massive saving in fuel costs compared to other similar sized boats. Incredibly, the vessel is performing equally well at light-ship as it does at full displacement, with only a slight change in speed or rpm.
Spirit of Hervey Bay took only 15 months to build. It was engineered by ATL Composites to meet Australian Standard USL 1C/1D. The hulls were strip planked in DuraKore over male frames while the remainder of the vessel was manufactured and supplied by ATL as a DuFLEX Component Pack, including hull topsides, tunnel, transom, bulkheads, soles, decks and superstructure. ATL Composites also manufactured and supplied lightweight non-structural panels for the ceilings and the fibreglass reinforcements used throughout. Their high performance KINETIX Professional Epoxies were used for additional laminating applications.
DuFLEX composite panels are available with cores of end-grain balsa, structural linear foam, cross-linked foam, or aramid honeycomb. These are all laminated using a high performance epoxy resin that is reinforced with multiaxial E-fibreglass or carbon fibre. The type and thickness of the core, fibre orientation and ply schedules are based on design or engineering specifications that are established around weight targets, stress and impact loads, and other design parameters.
To reduce wastage, ATL Component Packs have all parts required for the project nested together within the panels. These panels are sequentially numbered to indicate the correct joining sequence, and a nesting diagram detailing each part number and a description of it, is supplied for easy identification. The unique DuFLEX Z-Joint System, which allows the panels to be joined to full length parts, is structurally effective as tests have proven it to be analogous to a weld in aluminium.
ATL can engineer DuFLEX Component Packs to meet the rules of all major regulatory authorities, including Germanischer Lloyd, which recently recognised ATL with ‘Shop Approval for the Production of Composite Panels’.
[Sorry, this content could not be displayed]
For more information please contact:
ATL Composites Pty Ltd
www.atlcomposites.com
www.duflex.com.au
East Cape Marine Ltd
www.eastcapemarine.com
If you want to link to this article then please use this URL: www.sail-world.com/50483