Sailing Inspired Winning Antarctica Design
by Helen Hopcroft on 13 Feb 2007
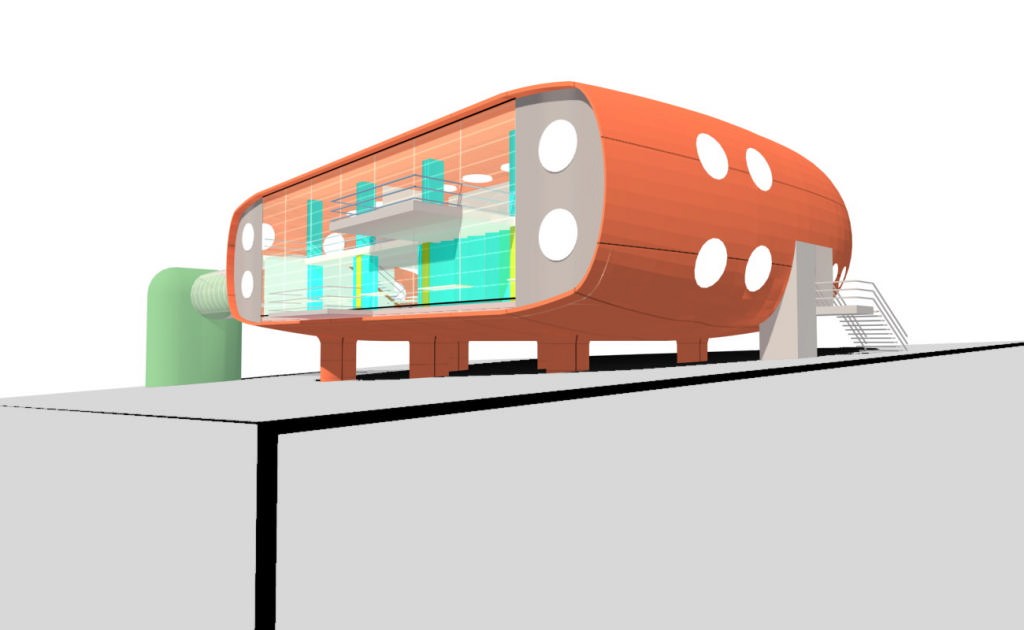
Antarctic design - inspired by sailing technology SW
Architect and keen sailor Michael Heenan was looking at the hull of a 90ft yacht when he experienced a Eureka moment. He was an entrant in an Australian competition to design a new building for the Davis Station in Antarctica. He needed to design a building that was extremely strong, well insulated and light weight. It turned out that it was his background in sailing that gave him the edge to win the competition.
In between his work as a director of the architectural firm Allen Jack + Cottier, Heenan sails regularly at a local, Australian National and international level. He also has experience coaching Olympic sailing teams. This year he raced in the Rolex Sydney Hobart on board David Forbe’s Merlin and the boat placed second in its IRC division.
He began by researching a range of building designs. He was looking for shapes that are extremely strong and for building materials that can withstand extreme climatic conditions.
‘I knew exactly what I wanted to do but I didn’t know how. I knew I wanted it to have the aerodynamics of a jumbo jet…the pressure capacity of the space station; I wanted to have the permanence and solidity of a submarine. I wanted the lightness of an eggshell and I wanted it to be as cheap as a hiking tent.’
He wanted to approach the problem of building in the Antarctica from a fresh perspective. At present most Antarctic buildings are constructed from 600mm deep universal beams with metal clad foam insulated panels. The interior has two walls of insulation and fire resistant plasterboard. Floors are concrete slabs. (Pouring a concrete slab in Antartic conditions is obviously a difficult job.) The buildings are solidly built to withstand the build up of snow and ice around their walls.
Heenan wanted to do something new.
Inspiration arrived as he was looking at a 90ft yacht hull. The hull was being constructed in Boatspeed’s high tech boat shed on the Central Coast of NSW, Australia. It was made of e-glass (a type of multi directional fiberglass), epoxy resin, carbon fibre and end grain balsa.
The hull was only 30mm thick, but when they subjected the forestay and backstay to 14 tonnes of pressure it only deflected about 3mm. He suddenly realised that he had found the perfect building materials for his Antarctica design.
‘It wasn’t until one day up at Boatspeed looking at this hull I realised that this is absolutely the perfect technology to create what I knew I wanted but didn’t know how to make’.
End grain balsa is an extremely strong, lightweight building material. The soft wood contains microscopic tubes of air called capillaries. The capillaries mean that the wood, which is more than 50% air, has good insulation properties.
Heenan explained why it is so strong; ‘If you think of a drinking straw it can bend easily. But if you have 30 drinking straws together and try to push the ends, they have incredible strength for the tiny amount of structure they’ve got.’
The balsa is used with the capillaries of air perpendicular to the outside wall of the structure. ‘You need that air to be vertical from outside to inside so that it’s got that insulation…. (It has) amazing compression qualities for its weight.’
His building design has extremely good insulation properties.
‘What I discovered was I could, using yachting technology, have incredibly high insulation. Almost too much…so I have to pump air into the building because it’s so well insulated.’
Having made the initial decision about building materials, Heenan approached the Brisbane based company ATL composites for their technical expertise.
Nicholas Cossich, Managing Director of ATL Composites described how they helped Heenan perfect his design and choose the best materials for the job.
‘ATL, in conjunction with Jutson Design, assisted the project engineers with composite materials engineering expertise and correct materials selection, based on environmental and practical fabrication considerations.’
‘The balsa specified for this project is BALTEKR SL.45 Superlight, a selected density product that offers excellent fire resistance – it does not sustain combustion, and has good sound attenuation, thermal insulation and excellent fatigue resistance, while still being a renewable resource.’
‘Epoxy resin was chosen for the dimensional stability it provides, impact resistance and its fatigue performance in high-wind environments…Wind turbine blades are laminated from epoxy resin for exactly the same reasons. ATL has a strong and successful position as an epoxy formulator and our versatile systems were developed for the construction of high-performance, lightweight composite structures for the marine, automotive, industrial, electrical, civil and tooling industries.’
Heenan’s sailing experience was also crucial to the design of the shape of the building. With yacht designer Scott Jutson, of Brindabella fame, he set about tank testing and wind tunnel testing a range of shapes. The design needed to be aerodynamic and able to withstand winds up to 300km. It also had to maintain insulation with temperatures dropping to -50C.
In the tank tests they used coloured crystals in the water to show the downwind shape of each design. The processes they went through were nearly identical to the techniques used in hull design.
He asked Jutson to be present at his meetings with traditional engineers. He found that the yacht designer had an intuitive understanding of where each design’s stress points were. He understood which areas needed to be built stronger to withstand increased load.
‘I love working with yacht designers. They’re just so innovative’.
Heenan describes the final shape as being like a ‘squashed wedge’ or like an egg cut in half longitudinally.
‘The shape is almost intuitively designed from the perimeters of the weather and the wind…Almost like you design a yacht hull’.
The final shape preformed well in the tank testing. But there were other factors to be considered;
‘I had to get the maximum volume in the space to be really frugal with materials. And so the (shape that has the) maximum volume is a circle. But a squeezed circle is the least breeze resistant. And then a squashed squeeze gets me back to nearly an optimum shape.’
The end result ‘faces into the wind like a wing’. The building is to be built in sections. Each section is constructed from a layer of carbon fibre, 2 layers of e-glass and then 200mm of end grain balsa.
Nicholas Cossich from ATL composites, described how the sections are constructed;
‘The structure is a combination of rigid end grain balsa, e-glass, carbon fibre and high performance epoxy resin, chosen as the optimum combination of materials to provide a suitable level of insulation and load carry capability in this type of project….’
‘The layers are laid down into a female mould and vacuum-bagged to deliver firm, evenly distributed pressure over the entire surface of a part, allowing a wide range and combination of materials to be laminated in one efficient process, resulting in thinner more consistent glue lines, with fewer voids and higher fibre-to-resin ratios. The part is then cured under heat in an industrial oven.’
Although the building is constructed from expensive laminates, the final cost of the building is relatively low. This is because the need for the heavy structural materials such as the 600mm universal beams is eliminated.
It is also because of the monocoque nature of the design. Monocoque means a structure where the chassis is integral with the body. An igloo is a monocoque building; a traditionally built house is not. In other words;
‘I use the skin to be the structure, the insulation, the coating, the sealant and the whole thing.’
Cossich explained the practical advantages of the building materials from a construction
If you want to link to this article then please use this URL: www.sail-world.com/31128