One Million Masks: Harken join a project to engineer, fold & sew over a million hospital-grade masks
by Harken 29 Apr 2020 07:00 PDT
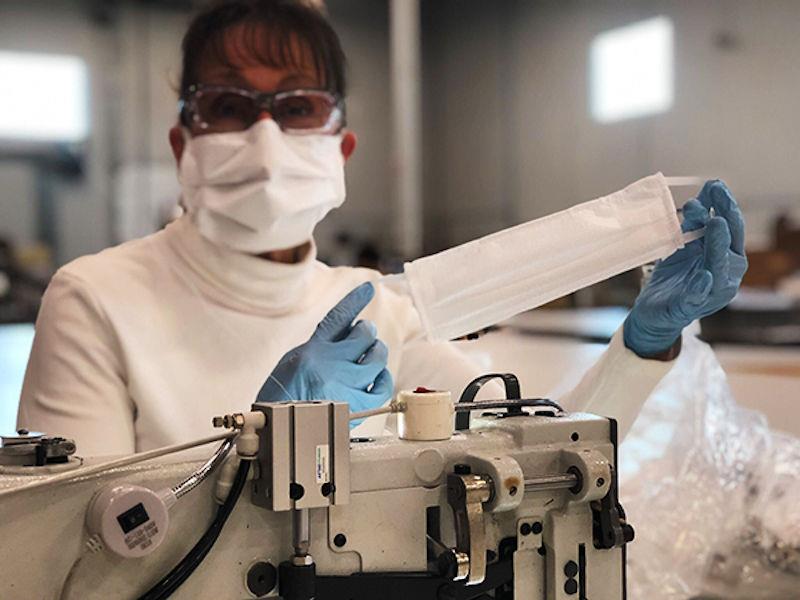
Harken join The Million Mask Initiative in Southeastern Wisconsin © Harken
Supporting those At The Front, Harken has joined a project to engineer, fold and sew over a million hospital-grade masks.
Our factory floor is teeming with healthcare initiatives right now - hospital-grade gowns, new engineering designs for N95 masks, plastic face shields, colorful cloth masks, and more.
The initiative to which we're dedicating the most firepower is an initiative called "One Million Masks."
To address the growing shortage of Personal Protection Equipment (PPE) for professionals in the medical field, we are active in a consortium with other regional businesses tackling a clear mission: build a million healthcare-grade masks. Many of these masks will be used in patient care environments in local Wisconsin hospitals such as the Medical College of Wisconsin.
Electrostatically charged at a high voltage to capture electrons in the fabric and increase filtration, these masks are made out of the same raw material as hospital-grade disinfectant wipes. This hydrophobic plastic polymer material doesn't harbor bacteria and is not permeable by water. "When people cough or talk, particles and droplets come out of the mouth, and they're stopped in the mask itself, so they don't spread into the air," said Dr. Christopher Davis from the Medical College of Wisconsin. These masks play an essential role as a bridge for healthcare workers waiting for the highly coveted N95 masks to arrive.
Our role in the One Million Masks initiative is to sew and assemble, a big task for a million masks. To contribute in a Harkenized way, we are dedicated to creating a systematic, repeatable process so the sewers and assemblers can be more efficient and output less waste. To make three folds in each mask, we were provided with a jig, and we needed to figure out how to make more - quickly. For accuracy of manufacturing, we digitized the jig and translated it into our design language so we could reproduce them fast. We needed to guarantee that the process would work well, so we made it easier to build and put a process together that would ensure Harken quality.
As the production model gets more stable and efficient, the consortium has become more optimistic about production quotas; now, the project has been upped to 3.5 million masks.
Working together inside our company. Collaborating with others outside the company to do important things. It's what we do most every day. Usually it's to make a boat go faster or help a responder make a trip up a rope safely. But this feels familiar. Harken Engineering. Harken Canvas. Harken Facilities. Harken Leadership. Harken neighbors and friends. Harken Volunteers. No compromises. No end to the commitment.