Making a traditional wooden flagpole with West System epoxy
by Suze Hart 10 Mar 2019 01:00 PDT
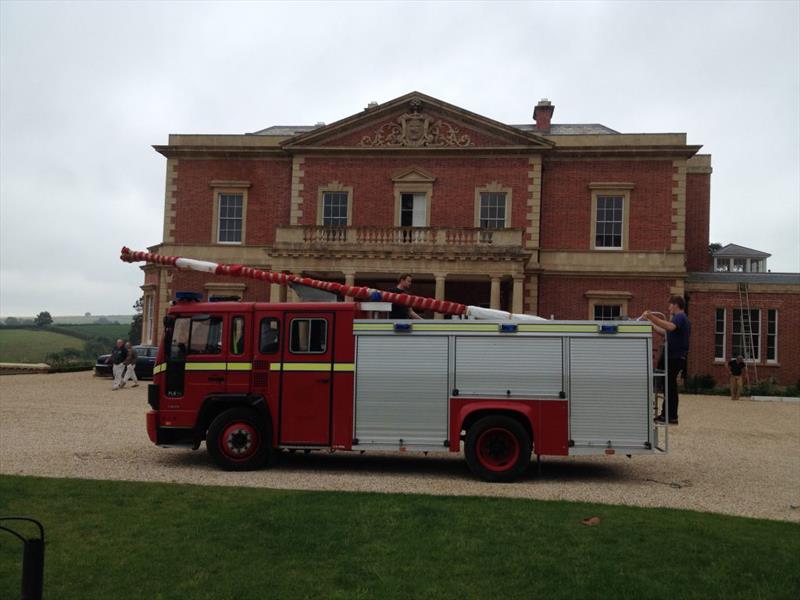
The Wooden Flagpole Company delivers with a decommissioned vehicle from the Carlisle Fire Service © Wessex Resins & Adhesives
If you were to see a fire engine drive past with a flagpole strapped to the roof you would be forgiven for being confused. Although an unusual choice for a company vehicle, the decommissioned appliance from the Carlisle Fire Service is ideal for the Wooden Flagpole Company to deliver and install its traditional wooden flagpoles.
The Wooden Flag Pole Company was born when owner Mark Stoddart was conducting a sales training day whist wearing his other hat of a cyber security recruitment director. One of the candidates who worked for a flagpole supplier told him that traditional wooden flagpoles were no longer available in the UK for historic buildings; so he decided to do something about it.
For the last 14 years Mark and his dedicated team have been crafting traditional wooden flagpoles for a wide variety of organisations and private customers who, it would appear, share his view that: "Putting glassfibre flagpoles on historic buildings is like putting PVC double glazing in Windsor castle."
The Wooden Flagpole Company, which uses WEST SYSTEM epoxy resin in all its flagpoles, operates from a workshop in Somerset, producing its poles using specially made lathes and jigs that they have developed over the years.
Kiln dried timber with a low moisture content is used to ensure that the flagpoles have a long life span "and will out live our customers." Although historically flagpoles were made from solid pieces of wood, Mark's poles are made by laminating the timber.
Aesthetically, lamination allows any knots or imperfections to be cut from the wood for a more pleasing finish. Practically, the longer lengths of wood that are needed are now harder to come by which was not an issue a hundred years ago. "Sadly, we don't have the quality of timber in the UK anymore and most of our timber is now imported from Europe," comments Mark.
The beams, 2-4m in length, are glued together using WEST SYSTEM 105 Resin and WEST SYSTEM 205 Slow Hardener. This lamination gives the length, strength and flexibility required. Mark says: "The woodworking adhesive that we use from Wessex Resins and Adhesives is just about the best that you can get for exterior and marine applications in fact it is so good that if you try to break the joint between two pieces of timber, the wood itself will fail before the joint does."
Once the lamination process is complete, the lathe is used to round the staff before being finished by hand. The square base, which comprises the first 1.5-2m of the flagpole, is planed and heavy chamfers cut by hand to provide an octagonal transition between the square and the cylindrical cross section.
The spars produced are unique in that a taper is created from the base to finial. The majority of flagpoles manufactured are cylindrical poles made from fibre glass many of which are not vertical due to the poor quality of the base fittings. A steel tabernacle, forged and welded in-house, and a pair of steel bolts supports the Wooden Flagpole Company's poles so that they stand straight and erect, but also can be lowered easily for routine maintenance.
The final step in the crafting process is to carefully sand the pole before applying several coats of the selected finish. The classic finish would be a white primer, two coats of undercoat followed by two coats of gloss. However, some customers prefer to see the grain and figure of the timber, which is achieved by applying just several coats of clear varnish.
Each flagpole is bespoke and produced to the customer's particular requirements. Mark's clientele spans many organisations and historic or listed properties including The National Trust, Historic Scotland and the RAF. "It is lovely to be able to contribute in a small way to keeping these buildings alive," says Mark, who enjoys bringing a project to fruition and working with such a tangible product, one that will stand the test of time.
One of the most challenging projects that the Wooden Flagpole Company undertook was for Bradford Live. This not-for-profit charitable company wanted to revamp the historic Odeon building in Bradford city centre, which had been derelict since 2000. Whilst waiting for funding it decided to replace the flagpoles on the copper roof domes to demonstrate all was not lost for the dilapidated dance hall that had once played host to The Who and David Bowie.
This was not just difficult logistically, with roads around the complex needing to be shut to provide access for the cranes to erect the flagpoles, but the crafting of the flagpoles themselves presented certain challenges due to their complicated dimensions. In the end a special 12m long lathe had to be fabricated specifically for the job.
It isn't just large organisations that employ Mark's services. Business, and indeed repeat business, also comes from discerning individuals. One gentleman in particular is a 'regular' customer with his third flagpole currently on order. The newest commission is for a castle the family has just finished constructing; after all, what would a castle be without a flagpole and finial?
WEST SYSTEM epoxy is also used on the flagpole finials from the Wooden Flagpole Company. The timber finials, made from special Iroko wood, are coated in epoxy to give them greater protection against the elements. Currently, only the finial is treated in this way, but Mark is going to be experimenting with covering the whole of the pole in WEST SYSTEM epoxy prior to varnishing to see whether it extends the maintenance window. Mark says: "We are now using more epoxy than ever but we don't just use WEST SYSTEM because of the quality of the resin. The customer service is fantastic and technical knowledge of the guys there is second to none; they are always on hand if we have a query."
Every flagpole is individual, made with passion and commitment to the time-honoured centrepiece. The option to insert a family time capsule into your flagpole and have an engraved brass plaque on the base also makes them an ideal present for the person in your life who already has everything; and as an added bonus it will be delivered personally, by Mark, on the back of a big red fire engine.
See more stories and tips at epoxycraft.com/category/blog