Making a 'smart' hotbox to store epoxy resin - Wessex Resins & Adhesives
by Jake Kavanagh 4 Mar 2019 01:00 PST
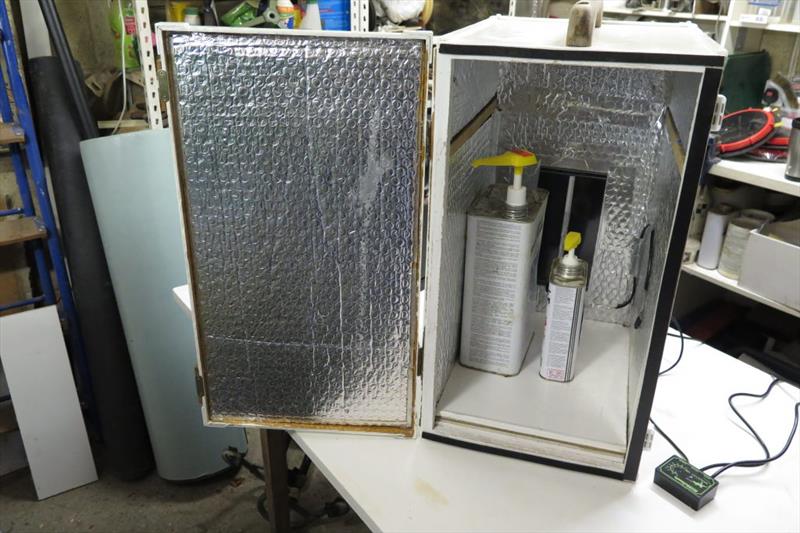
Insulating a box, fitting a thermostat and using radiant heat instead of a lightbulb saves energy and gives a stable temperature to keep your epoxy when stored in an unheated workshop © Wessex Resins & Adhesives
The winter is a challenging time for epoxy products. Warmth is needed to keep the resin fluid enough for the dispensing pumps to work well, whilst a cold ambient temperature can greatly reduce the curing times and may even compromise the strength of the finished work.
However, many of us are guilty of leaving our epoxy products in a cold garage or in the corner of an unheated workshop, so it's no wonder the epoxy comes out like treacle and can take considerably longer to cure instead of the usual two hours.
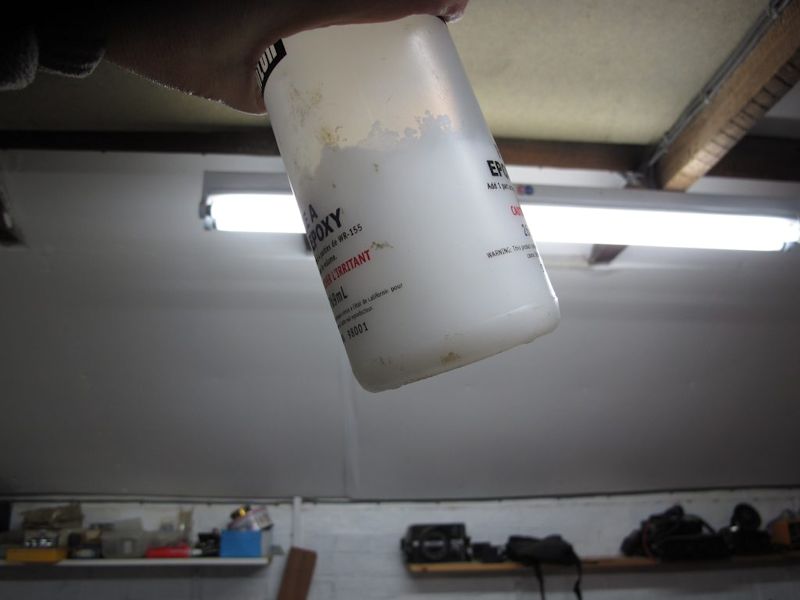
Sometimes epoxy resin can crystallise (during a warm-cold-warm-cold cycle) as seen here. The crystals can be returned to liquid by immersing the container in hot water and stirring the resin gently, being careful not to get water in the container. But its best to avoid crystallisation altogether by keeping the resin at a steady, warm temperature.
The answer is to make a 'hot box,' a plywood container with a 40-watt filament light bulb inside which is permanently left on and so keeps the box at a steady temperature (around 15-20 degreesC).
However, nowadays the standard filament bulb is being gradually phased out in exchange for far more efficient (but far cooler) LED equivalents. In addition, all of us want to save on electricity where possible and to minimise the risk of blown bulbs, especially if the hot box is being left unattended for long periods on a boat or other woodworking project.
The answer is to build a 'smart' hot box using standard, off-the-shelf, DIY electrics with simple thermostats. Also, after an idea from David Grey, we can swap the bulb for a heating element, specifically one designed for heating reptile tanks. Finally, rather than allow a steady flow of heat loss through the plywood of the hotbox, insulate it well so minimal energy is transferred in either direction. The heat stays in and the cold stays out.
It is easy to make a hot box using a basic electric jig saw to cut up a sheet of 6mm or 10mm plywood. The box can then be assembled using fillets of peanut butter consistency, WEST SYSTEM 105/205 epoxy mixed with WEST SYSTEM 406 Filler. If thicker plywood is used it can be nailed or screwed together. The image shows a simple version on display in the Wessex Resins training room. The hotbox dimensions should allow a WEST SYSTEM B-pack (5kg of resin and 1kg of hardener) complete with pump installed to stand at its full height inside. We suggest that a 30cm x 30cm x 60cm hot box is ideal.
Alternatively you can source a wooden packing case, tea chest or old wooden locker, often easily picked up at boot jumbles or from removals firms. Any wooden or metal container that can be enclosed could be used, but avoid plastic boxes as they can distort and give off toxic fumes when heated.
The first task is to add some decent insulation. Foam sleeping mats, which can be picked up for a few pounds from camping shops, are ideal. The dense foam is stuck down to the wood using DIY adhesives. 'Impact' spray glues are often used for this task, as they allow material that may be curved or distorted to be pulled flat by the glue. Both surfaces are sprayed, allowed to go tacky and then pushed together but some formulations are susceptible to weakening in warm temperatures.
For a really strong and dependable bond consider some WEST SYSTEM G/flex Five Minute epoxy which is excellent at bonding foams, rubber composites and other porous materials. Thickened WEST SYSTEM Epoxy also makes an ideal adhesive, especially as you are bound to have some as you are making a box for it! You will need to provide some sort of compression or weights if the foam is bendy to hold it down until the epoxy cures. (An old car battery works well for this.)
An alternative is to use a self-adhesive foam instead. This is costlier than a camping mat but very effective. The material shown here is for the insulation of GRP hulls or camper vans (RVs) and is 6mm thick, with closed cells (won't soak up moisture) and with a powerful adhesive on the back.
With the foam in place some standard silver coated bubble wrap from a household DIY superstore was added again, just a few pounds for a sizeable roll. This will reflect the heat back into the enclosure. Any excess was trimmed with a sharp knife in situ.
The edges were tidied up with some sticky-backed silver thermal tape. The bond was surprisingly strong. The tape can also be used to repair any accidental holes in the lining.
An old piece of PVC from a double-glazing job was used for the base but a trimmed and painted offcut of plywood or an MDF shelf would work as well. This ensures there is a wipe down surface under the tins should any epoxy be dripped or spilt.
The heating element came as a kit from a pet superstore and cost around £40. The element is flat and is designed to fit inside the cage and gently irradiate the reptile with infra-red, keeping the cold-blooded creature at a steady temperature.
To ensure the poor thing isn't cooked, a temperature probe (in the right hand) connects with a thermostat (left hand) the latter located outside the box. This can be set to the ideal temperature, although the reptile has to leave the operator to work out what that is. For epoxy, the sweet spot is around 20 degreesC.
The irradiator was mounted using silver tape at the back of the box and the leads taken through to the outside. You might need to do surgery on the wiring to tidy it up and shorten the leads a bit.
The sensor was set quite low down. This is because any crystallisation of the resin will happen at the bottom of a tin of epoxy, so you want the 20 degreesC warmth to penetrate right to the lower part of the box. Only then should the power shut off. The sensor was positioned and held with thermal tape.
The lid to the box was also insulated, fitted with a pair of hinges and two magnetic catches were added. The whole box was also painted white but that's just an aesthetic detail. We also added a carry handle, as it would need to be hauled up some steep steps to get it on board.
Now up and running, the 'smart hot box' should keep a steady temperature within the box with little loss of temperature. Note the batons at the top allow the fitting of a shelf for smaller items, such as tubes of sealant or other temperature-sensitive products. Energy draw in is minimal, which is just as well as electricity to the hard standing is individually monitored for each project.
If you have made a hotbox or similar enclosure, Epoxycraft would love to hear about it.
See more stories and tips at epoxycraft.com/category/blog