Speedboat takes advantage of Southern Technology
by Richard Gladwell, Offshore Yachting magazine on 10 Jul 2008
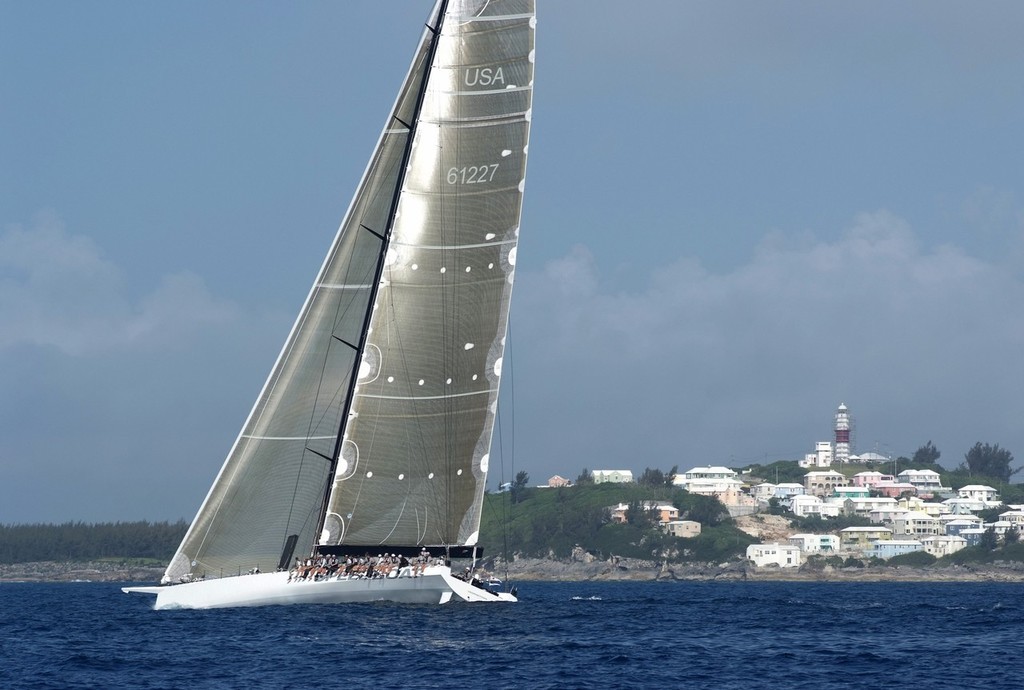
Speedboat approaches St David’s Light at the finish of the of the Newport to Bermuda Race. PPL Media
http://www.pplmedia.com
Soaring an impressive forty six metres above the Viaduct Basin in downtown Auckland, Speedboat’s rig represents the new leading edge in spar and rigging technology.
Constructed a few metres away in Southern Spar’s factory in nearby Pakenham Street, the state of the art carbon spar is stepped aboard the most powerful racing yacht in the world.
The movement of large high tech carbon spars on trolleys through waterfront streets, has become a commonplace sight. Southern Spars is located in the heart of the traditional ship servicing areas of downtown Auckland. Since the loss of the America’s Cup, the western waterfront area has taken on a new life as a unique large yacht servicing facility.
Speedboat, from the board of in-vogue Argentinean designer, Juan Kouyoumdjian, and built by Cookson Boats, is the latest of a an exclusive breed of 100ft long supermaxis.
These are the fastest racing monohulls in the world, which generate their enormous stability from the use of canting keel technology. Most pundits tip Speedboat to take over the mantle of the planet’s fastest monohull, and to shatter many race records along the way.
'With Speedboat, we had to work with loads that we had never really imagined', explains Southern Spars Project Manager Ilan Graetz. 'To give you an idea, the masthead load on the halyards is about 20 tonnes. In order to be able to handle that sort of load we had to engineer special locks – as that is the only way we can cope with those loadings.'.
Close your eyes a little, and Speedboat’s lofty black spar takes on a distinctly dinghy like appearance – reflecting the sailor’s fetish for drag reduction and enhanced aerodynamics.
'We’re looking for as little drag as possible,' explains Graetz .
'One of the things that has helped us to achieve that goal is the new EC6 (Element C6) carbon rigging, which is manufactured by Southern Spars Composite Rigging Division in Newport, Rhode Island.'
'The secret of the EC6 rigging is not that it is smaller in diameter but that it has greater tensile strength. The most important thing for us in rigging, is to reduce stretch.
'We have also eliminated all spreader fittings, by developing a single rig harness', he adds.
'Rig harness' is perhaps a term that needs some explanation, but is at the heart of the EC6 system
The concept of continuous rigging is that you have a bundle of small diameter rods that start from the bottom, then at each spreader, one part of the bundle splits and is directed to the mast wall to form the diagonal.
When removed from the mast, the rigging on one side of the mast all appears to be from a single piece of cable, comprising a single-sided herring bone with the main stay being the backbone and the diagonals branching to the same side.
Ilan Graetz again: ' The diagonals are as well as the verticals continuous from the top to the bottom of the rig. In order to reduce the diameter of the combined vertical and diagonal diameter at the bottom, we taper some of rod of the diagonals as they join into the verticals, this allows us to reduce the overall diameter of the verticals.'
If you trace a component rod strand from the point where it joins the chainplates, some will run to the top of the spar, others will run part way up the mast to form diagonals, however they all start from the same base point.
In pursuit of the Holy Grail of drag reduction, the EC6 carbon continuous rigging requires only the simplest of notched spreader ends, and a piece of lashing, to hold the carbon cable in place. The end is finished with tape.
Gone are the multiple pieces of stay, turnbuckles, cap fittings. Instead there is a single piece of cable which splits away into various diagonals at each spreader and passes through a carbon ferrule in the spar before being secured internally.
As mentioned before, rather than being a solid piece of carbon, EC6 rigging is constructed from a bundle of small diameter carbon fibre rods. The rods are then bound and are jacketed with a choice of materials to protect the rods from chafe and impacts.
The EC6 technology is not new, having being first fitted, as discontinuous rigging, to the Farr 52 Georgia over four years ago. Since then it has been installed on a variety of yachts from 30ft sport boats to 50 metre superyachts. The Farr 60 NUMBERS was the first racing yacht to be fitted with continuous rigging in 2005. To date there have been no failures.
All except one of the 2008/09 Volvo race entrants will be using Southern Spars and EC6.
Virbac the winner of the Barcelona double handed round the world race used EC6, which was destruction tested after the race and broke at 110% of the designed load.
The rigging technology is available to other spar makers. For instance, one of the Volvo racers is using Hall spars and EC6. The rigging system can also be retrofitted to existing spars.
Unlike wound fibre cables which can unravel, the nature of the EC6 rods are such that the strength of each constituent rod remains - even though others around it may have been damaged through extreme chafe or severe impact. Comparison of EC6+ with other composite rigging products reveals a drag reduction of about 12%.
End fittings at deck level are another area for significant reduction in windage and drag with the constituent rods being spread, fixed in epoxy resin and moulded to accept a tapered female end fitting.
'The major improvement in the last year has been the interface between Southern Spars and North Sails, where the two organisations have interfaced their respective design and structural computers so that the programs RigCalc and Membrain work together to perfectly match sail design to spar performance', explains Graetz.
'To give you an example, with a boat like Speedboat, we do our initial tuning and setup on the dock, and then go sailing.
'Speedboat was launched on the Tuesday night. On Wednesday the five spreader mast was stepped and tuned, and the next day, Thursday, at 11o’clock we are out doing 29kts in the Hauraki Gulf! There is nothing more to do, because once the loads are properly set up, the rig is properly tuned for the sails.
'We get an output from RigCalc and Membrain and use hydraulic jacks for every step of tuning from the bottom up. We target the check pressure that we want to have at the mast base and progressively work up, to set the rig up. We can manage the loading and pressure for each stage rig back to the mast and sail programs in the Southern Spars and North Sails design computers.
'All we would do with more time is just to check the rig, and fine tune it, in different weather conditions.'
One of the unique features of Speedboat is the deck stepped mast which uses a ram on the forestay - allowing the rig to be racked from one to five degrees, just like a dinghy. The mast rake can be adjusted while the supermaxi is sailing.
Looking back over the last three years, Graetz lists the main advances in carbon spar technology as being the refinement of the laminate drawings and the whole Membrain and Rigcalc interface that has allowed Southern Spars to pinpoint where rigs have to be stiff and how to achieve that.
'Now we are running rigs that are significantly stiffer than they used to be. The quality of the carbon has improved where we now use ultra high modulus carbon in the mast section. We have also been able to save a significant amount of weight out of the rigs, and have reduced drag as well.
'Another significant development is the use of halyard lock technology and the development of internal halyard locks. The locks are much more user friendly and the reliability has improved greatly', he adds.
[Sorry, this content could not be displayed]