Resin Infusion Program
by Brent Vaughan on 30 Jul 2007
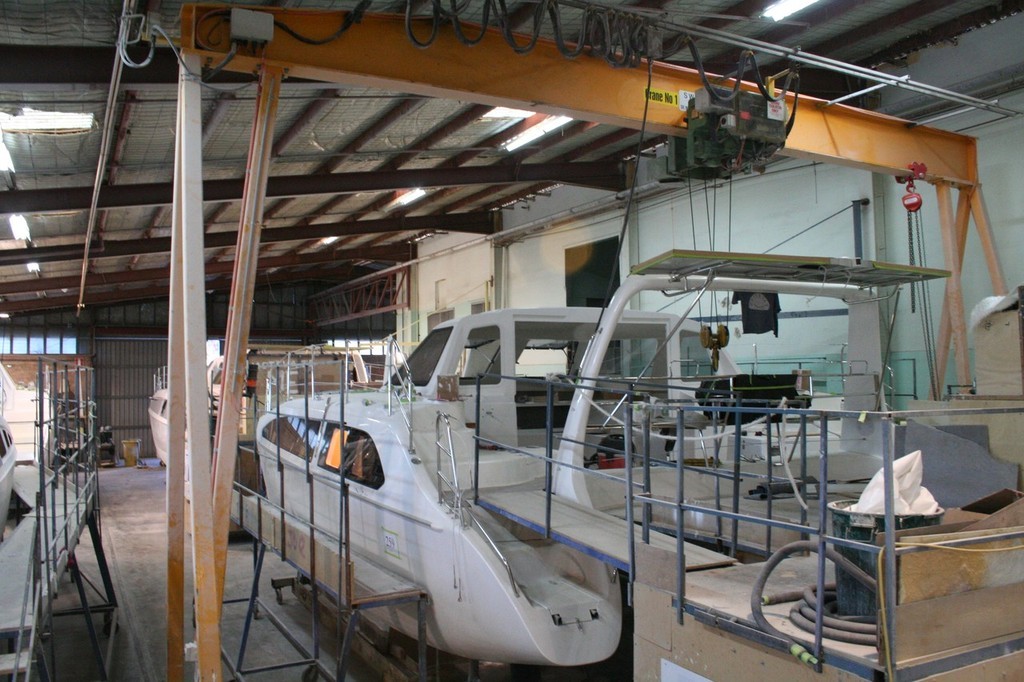
Seawind Production Line Brent Vaughan
With a long list of forward orders for both the new Seawind 1160 and the popular Seawind 1000, Seawind are continually working on ways to streamline production and improve manufacturing methods that will ultimately increase the output of boats each year. As a result, Seawind are now in the process of transferring from conventional fiberglassing methods to the revolutionary Resin Infusion method.
Seawind's Development Manager, Tim Makepeace, visited New Zealand attending a Resin Infusion program run by High Modulus and conducted by some of the most experienced consultants in the world on the subject. Richard Hallowes who has specialised in the field provides an insight to this new technique offiberglassing boats.
What is Resin Infusion?
Resin Infusion is an exciting new technique aimed at greatly improving all aspects of fiberglass
moulding production. Totally unlike the traditional open mould style of fiberglass boatbuilding, resin infusion is a closed mould technique designed to greatly improve every aspect of the lamination process.
The conventional method of fabrication involves placing the glass fabric in an open mould and saturating each layer of glass with resin, layer by layer, and consolidating by hand using brushes & metal rollers. This method is time consuming, labour intensive, messy, smelly and directly exposes the fiberglass operator & the environment to the chemical properties contained within the resin.
With resin infusion however, the glass fabric is placed in the mould dry. A PVC 'vacuum' bag is then placed over the mould, sealed around the edges using sealant tape and the air inside the bag/mould is evacuated using a vacuum pump. Resin is then drawn into the mould, using strategically placed pipes, under the influence of vacuum pressure, wetting out the dry glass fiber in the mould and is then left to cure. After which the bag can be removed and the part extracted.
Sounds simple in principle, the difficulty arises in the strategic positioning of inlet hoses/vacuum lines/flow media as well as gel times etc.
How does this technique improve the structure of the boats?
There are several advantages to moving to resin infusion.
a. The parts are of a higher quality with less air voids and better dimensional tolerance.
b. The part quality is repeatable time after time as the inconsistency of the individual laminator is removed.
c. The part is lighter as better fibre / resin ratios are achieved.
d. The working environment is cleaner as the operators are not directly exposed to resin (this is
particularly important as tougher laws regarding air quality and occupational health come into play.)
e. Part turnaround is quicker as there is only one cure as opposed to the multiple cures of a conventional hand laminator part.
What are you currently working on in the Seawind factory?
At the moment we are infusing the Seawind 1160 Targa and just recently started on the forward furniture units which are quite complex.
If you want to link to this article then please use this URL: www.sail-world.com/36156
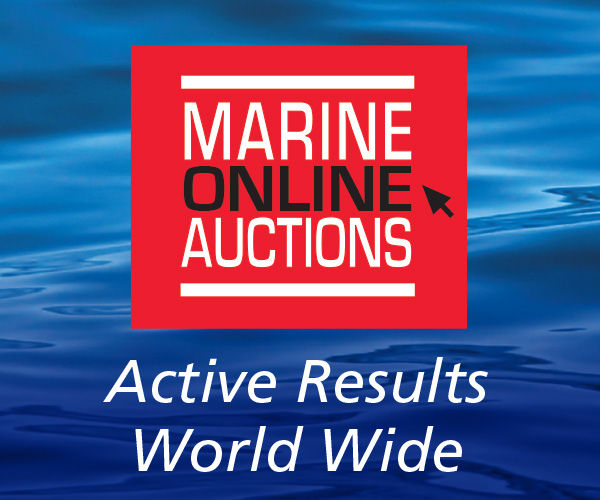
-202310120654.png)