RS100 case study - reprinted from SeaHorse magazine
by Seahorse Magazine on 27 Sep 2011
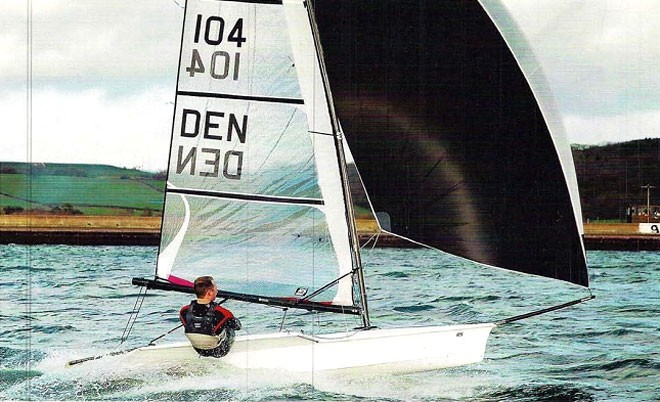
RS100 on the water Seahorse Magazine
http://www.seahorse.co.uk/shop/subs
It’s a process that began with the Laser in the 1970s, small boat racing is increasingly devolving to manufacturer-led classes.
Some have been more successful than others but RS Sailing have rarely faltered in continuing to produce fast, modern and attractive designs that quickly acquire a strong following.
The company's latest number, the RS100 single hander, set a new benchmark by attracting 120 orders before launch...Martin Wadhams and designer Paul Handley look at how a major manufacturer like RS comes up with a concept for a new class, the development process and how the final product eventually emerges.
Concept stage: 'The RS100 first appeared on our agenda at our annual international dealer meeting in October 2007,' says Martin Wadhams, Managing Director of RS Sailing. 'We had picked up on significant bar talk about the hole in the market for a more attainable, modern, performance single hander.'
Through 2008, the RS team kept their ears to the ground, wanting to be sure there really was a demand for a new class. RS director Nick Peters and Production Director Alex Southon began to build up a brief for the boat they felt would suit the market, working closely with Naval Architect Paul Handley. First step in this process for RS is always to define the market as tightly as possible. The RS100 target market was summarised as:
-Singlehanded dinghy sailors who have done the same thing for years (for example, Laser sailing) and would like a new interest.
- Sailors who have tried modern boats such as the RS700, Musto Skiff and Moths and found them too difficult, too complicated or too expensive, but who would like to race a modern boat.
- Doublehanded asymmetric sailors who find it difficult to sail regularly and with the same crew.
- Keelboat racers keen on some convenient excitement in between other sailing commitments.
The next step in the process involved creating a design specification, with input from the international dealer network giving a global view. Key elements of this process included:
- Target prices: Having decided the £7,000 UK retail price felt acceptable for the market the team worked back to calculate the target Bill of Materials cost and broke that down into individual component costs to achieve it.
- Materials: The BoM cost allowed for an epoxy/GRP/foam sandwich hull – which RS wanted to achieve for light weight, stiffness and long lasting performance. Carbon spars -again seen as essential for their light weight and dynamic response to deliver the performance desired.
Key features: Gennaker-considered essential for the excitement factor and to provide a major step forward from
conventional single-handers.
Centreboard -Chosen over a dagger board (in one of the most contentious decisions). A daggerboard case is simpler and easier to manufacture, and the short slot creates less drag with no need for a slot gasket. But a centreboard is much more user friendly when launching, and reduces damage if you run aground at pace. This decision was later borne out almost unanimously by the response in several rounds of sailor feedback questionnaires.
Moulded in wings - to give the righting moment required for power and speed, without the cost and complexity of
'Bolted-on' wings.
Handling Requirements: Speed vs. stability - put simply, narrower waterline faster but less stable. A maximum waterline width of 900mm with a fine entry at the bow was selected to give the balance wanted.
Wider deck/wing = faster but less stable; more leverage gives greater righting moment and sail-carrying power, but go too wide and the boat becomes unstable, especially in gusty conditions. A maximum width of 1,830mm was selected with manageable e handling seen as more important than extreme speed for this boat.
Light vs. heavy-wind performance - More rocker helps keep the stern from dragging and increases light-wind performance (especially for heavier sailors), whereas a flat rocker aft provides higher top-end speed. Everyone was clear that this boat should perform well across the wind range, so more rocker was agreed on than is typical for modern skiffs. The team were sure that a light, easily driven boat with one person and two sails was going to be quick enough downwind for most aspirations in a breeze-and the additional benefit of rocker aft is to lift the bow at speed, reducing pitch-poling and making a wild kite ride more enjoyable.
Design stage: With derailed briefs in place, Paul Handley developed computer drawings of a hull and deck shape in early 2009, with significant dialogue backwards and forwards between RS and the designer about the matching of the design elements to the brief.
RS decided to produce prototype hulls using a system that they had not tried before. Hythe-based Choose Design offer a service that involves the CNC milling of temporary moulds from a large laminated block of MDF reconstituted wood. These moulds can then be used to make up to around six hull and deck mouldings, with the benefit that all the sailing testing would be done on moulded hulls which would feel more like the real thing. Equally important, the boats would be built using normal production methods, so resting of the build specification would start from the first prototype.
The prototypes also looked more like proper boats, giving a better indication of the final appearance. Making prototypes this way was more expensive than traditional methods, which placed greater importance on getting close at the outset to the final design from a style perspective.
The plan to build the prototypes with Choose Design led to two further decisions: The first, to approach a product designer for styling input; the second, to get Choose also to mill a quarter-scale hull model so that the appearance of the hull could be closely debated in three dimensions.
Italian product designer Daniel Vitali used to race an RS600 so RS felt he would have a practical understanding as well as the right design skills for the styling job. Vitali's contribution did not change any of the fundamentals of the design, bur several of the seemingly minor styling contributions that he added have undoubtedly contributed to the cohesive good looks of the final boat. As Wadhams puts it, 'A boat first needs to function correctly and if you can combine that with great looks, why wouldn't you? There's nothing revolutionary in that - especially if you happen to work for Audi.'
Prototype stage: Paul Handley supplied the computerised design files to Choose Design in April 2009 and they milled the moulds and built the first hull by the start of June.
During this period Selden produced the first draft set of carbon spars. A new rig system had been designed, with shrouds and spreaders, but no forestay. This allows the mast to bend almost like an unstayed rig upwind, with the resulting gust response and adjustability, but the shrouds and spreaders prevent the mast inverting and bending forwards downwind under heavy gennaker loads. RS feel this is crucial to prevent the bow being driven down, and to keep the hounds to bowsprit tip measurement constant so that the gennaker luff remains the correct design length in all conditions.
This is a new rig system in itself and to complicate matters Peters and Southon were both keen for the mast to rotate for aerodynamic efficiency, so Selden purpose designed a new, two-part spreader bracket which allows the mast to rotate inside it.
Mike Lennon of Hyde Sails, RS's long standing sails partner, produced the first sail designs. You will notice the plural here- from the curser RS had heard from both light and heavy sailors that they really wanted this boat to work for them, hence the target sailor weight range of 70 to 1OOkg. After examining all the options, the design ream concluded that the purest way to achieve this was with two mainsail size options -as per the Laser and Laser Radial.
Width-adjustable equalisation systems would have added complexity and cost, and RS were already getting the feeling that the marker for the 100 could be big enough to mean that splitting the racing fleet would not be a problem. So Lennon produced two mainsails, with square heads chosen for their efficient tips and modern appearance.
Prototype development: On-the-water resting began in early June 2009 and the immediate reaction was positive. 'The boat felt manageable, responsive and very comfortable to hike,' says Peters. As expected, there was work w do to achieve the correct combination of mast stiffness and mainsail luff curve (this still seems to be a relatively trial and error process) before hull and rig development could progress in detail.
DESIGN NOTES: 'length 4.3m Beam 1.83m Hull weight 55kg Sailing weight 80kg Hull & foils epoxy/foam sandwich,.
Mainsail_areas 8.4mand lodm• Spinnaker-area 12m2/Spars carbon epoxy Designer Paul Handley
The RS 100 design brief was for a modern singlehanded hiking dinghy with asymmetric spinnaker suitable for a broad range of crew weights. The boat was to be fast and exciting off wind but not at the expense of difficult handling and with good performance in both light and heavy airs to ensure that it would be a good all-rounder In the hands of typical club sailors as well as experts
RS had decided to announce the RS100 project as soon as they were happy the prototype was on the right lines and take the bold step of running a very public development programme. They created an online blog charting the progress and decision making process, as well as inviting a large number of sailors to sail the prototypes and give their detailed feedback.
'There were so many ways one could tackle the modern singlehander concept,’ according to Peters. 'We really wanted to know if a wide range of sailors felt we were progressing along the right lines through the development process.' In truth, this publicly developed idea captured the interest of sailors around the world and gained a life of its own.
You can still view this development blog via a link on the RS100 page at RSsailing.com - which demonstrates clearly and publicly how every aspect of the boat was tested, assessed and refined. The hull shape worked well from the outset and the only tweaks made were to widen the chine width at the stern by about 15mm each side and drop the chines at that point by 10mm- to improve water release at high speed and in waves.
By far the most time-consuming aspect of the development centered on the rig - absolutely critical to successfully creating a good one-design Sailboat. Interestingly, although everyone liked the appearance of the big square bead sails, they just couldn't be made to work as well as narrower heads on this hiking singlehander. They raised the centre of effort and overpowered the boat more quickly for a given area, without enough efficiency gain to reduce the area to compensate. So a more conventional roach profile was eventually selected.
The layout of the cockpit and fittings is very simple which actually took longer to achieve than a complex fit-out. A sophisticated injection-moulded deck plate was produced, incorporating an adjustable mast gate for rake control, and under deck concealed turning blocks for the vang, Cunningham and gennaker halyard. An injection-moulded bow plate was also designed to act as the top bearing for the bowsprit, incorporating a track underneath for the forward end of the chute sock. The mainsheet jammer turret incorporates the centreboard up haul down haul systems and spinnaker halyard clear.
Alex Southon, who designed these fittings, says, ‘We’ve tried to move the game forward. By custom-making the fittings they perform multiple functions and also look good. Little things make a difference- for example, if you sight along the curved foredeck, the bow plate shape follows the deck itself perfectly.'
Tooling stage: Choose Design produced the final hull and deck plugs which were air-freighted in September 2009 to Composite Marine International (CMJ) in Thailand who were to build the boars for RS. CMI is run by two experienced British composite race boat builders - Pom Green and John Higham - and has the advantage of a skilled, low-cost labour force. Along with some much larger designs, CMI already produce several other RS models and RS employ their own quality control manager who is based full time at the CMJ facility.
By this stage RS had taken over 100 preorders from around the world for the RS100 and so CMI have built three complete sets of moulds to meet expected requirements. The first production boats were built in late 2009, with production rate planned to rise to a maximum of 30 boats per month by spring 2010. By the end of the London Boat Show launch in January over 130 boats were spoken for in the production schedule, proving beyond doubt the excitement and demand for the new boat. The first major international RS100 regatta is scheduled to take place on the Cote d'Azur in September this year.
Perhaps the world really has been waiting for the next big thing in singlehanded sailboats.
Republished courtesy of Seahorse Magazine website
If you want to link to this article then please use this URL: www.sail-world.com/88958