Traveller repair- Turning a $2000+ replacement into a $360 repair
by Vincent Bossley on 11 Jul 2011
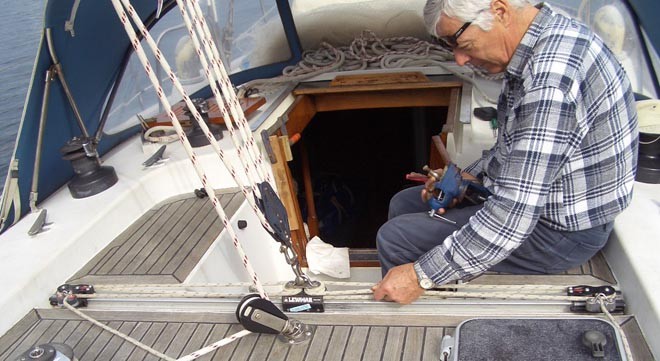
Traveller repair SW
Vincent Bossley here describes how a little perseverance and ingenuity, together with some pleasant time in the sun, turned a $2000 replacement into a $360 repair: The mainsheet traveller on a friends 43ft (13mtre) sailboat was showing signs of wear. The traveller was installed on the yacht when it was built and so now was twenty two years young.
The traveller track itself was still in good order but the bearings inside the car were beginning to disintergrate. When you consider the constant pressure on these bearings when under sail over the years and many many thousands of sea miles, it is not surprising that at some point they will require some attention.
The symptoms of course were that the traveller was wanting less to slide and becoming more difficult to shift and generally getting more stiff - which in turn becomes more of a handicap when sailing.
The starting point was to take down the headlining in the aft stateroom and head/shower cubicle underneath the traveller. Let me tell you from the outset that this was the most time consuming and awkward part of the job. Always working in a confined space, the temperature rises along with the fiddly nature of the work.
This part accomplished we moved topsides to remove the sheet lines from the traveller block and sheave of the traveller and secure the boom off. this meant that the car could slide freely along the traveller rail. All eighteen heavy duty screws were removed from the traveller rail so we could then lift the rail away from its position. The end caps were prised off so that we could then slide off the car. As you can see from the image, the bearings (four each side, totalling eight) were in pretty bad shape with constant wear and corrosion over time having taken their toll.
In preparation ahead of time new bearings had been located which were five millimetres underwidth of the old ones. The reason here was that the difference in diameter was to be made up by pressing on a composite material called Delrin (Semi-Crystalline Engineering Thermoplastic). This was done by a local engineering company for a paltry sum of $20.00 including a spare set! The bearings themselves came to $246.00.
These were easily placed into position on their pins and the car slid back onto its rail. The track was then firmly remounted in its position on the bridgedeck. Two Ronstan deck organisers were purchased at $50.00 each and positioned at each end of the track and using the existing camcleats. The lines were fed back through and the car tested for smoothness of operation. Needless to say, it worked beautifully and with the composite 'Delrin' material the car ran very smoothly.
Apart from time, the all up cost of the job of bearings, Delrin press-ons and sheaves was $366.00. The replacement cost of a new traveller system from the manufacturer was $2000.00+. So, we felt we were well ahead and even if it were to wear again say in five years time, there is a second set of press-ons available.
The boat has been out sailing - and racing - several times since the refurbished car and traveller was refitted and to date is performing very well indeed. Composite materials are used so widely these days, especially so in sailing and yacht building that there is no reason to suspect that the Delrin coated bearings will not give many years of sterling service.
You can read more about sailboat equipment servicing, maintenance and refurbishing in Vince's ebook 'Voyage of the Little Ship Tere Moana' downloadable, and then there's the very handy publication, '101 Dollar-Saving Tips for Sailors', both available by http://www.sailboat2adventure.com/!clicking_here.
If you want to link to this article then please use this URL: www.sail-world.com/85741