North Sails Technology advances with 3Dr
by Rob Kothe on 15 Aug 2006
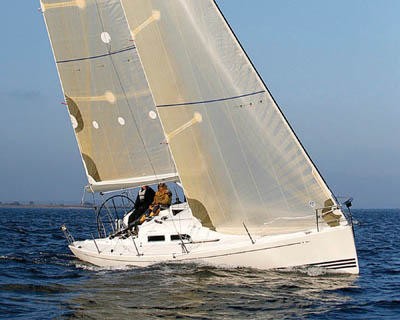
3DR-X35 72 SW
The largest sail maker in the world, North Sails has been using a three dimensional 3DL™ manufacturing process to mould sails into a single, seamless piece since the early 1990’s.
However world wide demand for sails made using the 3DL process has meant extensive delivery lead times in spite of considerable expansions in manufacturing capacity.
Now another technology break-through with the long awaited start of rotary moulded sail production at North Sails Toronto (Canada) 3Dr facility, will shorten delivery and allow smaller keelboats and one-designs access to three dimensional moulded sail technology.
This project has been far from plain sailing as Executive Vice President Jay Hansen explains. ‘The fact is historically North Sails has always been ‘a little bit crazy’ I would say in terms of its use of technology. And this 3Dr project is absolute proof.’
Jay related the history of the sail maker’s 3D products. ‘In the 1980’s we made panelled sails. At the time we were one of the few sail makers that actually shaped the seams of all those panels; most sail makers would put them together flat which was far easier, it didn’t make quite as good a sail, but it was far easier.
‘We began discussions about three dimensional sail manufacturing in 1989 with J.P. Baudet and in 1990 we began development.
‘The first prototype 3DL sail was a J/24 genoa. The sail held its shape, even in strong winds and stood up well to wear and tear. It was also 33% lighter than a traditional panelled J-24 headsail.’
He continues, ‘Comparing the 3DL product to our own panelled sails, which we could do in hundreds of cases, we quickly realised the 3DL product was far better than we expected it would be. We learned the reason why, was that each individual yarn in a 3DL product was doing a more efficient job, yarn by yarn, than it could do in any kind of panel sail. Not because it was continuous but more because it was lying in a three-dimensional plane, something it could not do in a panel sail or in other two-dimensional sails. The big different was 3D versus 2D.’
In the North’s 3DL system, a computer numerically controlled head applies high-modulus kevlar aramid yarn onto the surface of a Mylar film, on a three dimensional mould. The head lays down a yarn pattern that follows anticipated loads in the sail. The yarns are applied under uniform tension and adhere to special glue that coats the surface of the film.
When the application of the high-modulus yarn is complete, a second layer of Mylar film is applied over the top. The laminate is then pressurised through vacuum bagging and heated to cure the laminate.
Weight savings are achieved principally by more efficient application of the yarns. The 3D process uses less yarns than a 2 D ‘string’ sail.
The result is a one-piece smooth sail with no seams that holds its designed shape over a remarkably wide wind range.
Since 3DL was introduced, steady growth in worldwide demand has driven constant efforts to increase 3DL production capacity.
The largest sail maker in the world, North Sails has been using a three dimensional 3DL™ manufacturing process to mould sails into a single, seamless piece since the early 1990’s.
However world wide demand for sails made using the 3DL process has meant extensive delivery lead times in spite of considerable expansions in manufacturing capacity.
Now another technology break-through with the long awaited start of rotary moulded sail production at North Sails Toronto (Canada) 3Dr facility, will shorten delivery and allow smaller keelboats and one-designs access to three dimensional moulded sail technology.
Jay explained this demand led to the quest for a faster and more efficient manufacturing method. ‘From the beginning of 3DL we realised the labour content was still quite high and it was a relatively expensive sail to make, even though the process made a better sail.
‘As far back as 1991 I said to Bill Slyne of Industrial Evolution, Inc. in Toronto, who worked on the original 3DL system, ‘ Bill, see if you can figure a different way to make this sail, we now know the product is right. We just need a machine that will make it faster and more efficiently.’
‘In 1997 he called me one day and said ‘I’ve got it!’ I have to confess when he called me and explained it I couldn’t understand how this machine could possibly work and nobody in the company did. With some demonstration we realised that it is a brilliant idea, which frankly it really is.
‘The 3Dr project has been a very long, and I must admit, a very difficult project and I would say that the difficulty comes as a result of the extremely complex nature of the machine.
‘Possibly if I knew what I know today I might not have recommended we pursue it, which would have been a mistake.
‘However we have achieved the result and I can safely say that there is no sail making machine in the world that comes even close to the productivity of this machine. The breakthrough is parallel processing with all the elements of production occurring at the same time. With other manufacturing processes it’s a serial method where you go one step after another.
‘In some ways it is an insane project and I think that a lot of businesses would have stopped it at a certain point and said, ‘this is not going to be economic this is not going to work’ but at North Sails we are so fervent with technology and so strong in our belief that we have to rely on technology both for product and for process. Ultimately you have to keep your costs down as you can’t create a system that is expensive, as clients want value.
‘We are extremely happy now. In essence we had to do it twice. In 2002 we completed a machine called the RM4, which was four metres in length and it worked, but not well enough.
‘It produced about 300 sails, but of the 300 sails I would say maybe 50 of them were good and useable. That is not a very good ratio, obviously. But we did not stop, we analysed the problem areas and went again.
‘The same crew that built this latest machine built the prototype for Boeing Aircraft that has allowed Boeing to make the decision for the 787 fuselage to be carbon fibre.
‘What is interesting about it, is if you say to a layman ‘we are going to make a machine to make a Boeing 787 carbon fibre fuselage’, compared to saying ‘we are going to make a machine to make sail making blanks’ one would think that the Boeing project was much more difficult.
‘But in fact it was much easier and took far less time. I am not saying it wasn’t difficult, but relative to the 3Dr Rotary Moulding machine it was actually quite easy.
‘It’s been a long haul and a sizeable investment for North Sails, although finally this amazing machine is producing sails each and every week,’ says Jay.
‘The 3Dr machine will produce smaller sails at about ten times the rate of the 3DL moulds. This will allow us to increase sail production capacity for larger sails on the 3DL moulds.
The 3Dr Rotary Moulding process first combines film, fibre and scrim materials over a three-dimensional moulded shape, then bonds all three using heat, vacuum pressure and special adhesives. Because the three-metre diameter drum rotates during the process, the mould surface is adjusted continuously to conform to the sail’s designed shape using 2,200 computer-controlled pistons located inside the drum.
‘In the first stage of manufacturing, Mylar film is fed into the machine. Strands of glue-infused aramid fibres are laid on the film in continuous thread patterns as the drum rotates. After the tensioned fibres are placed on the film in predicted load paths, another layer of Mylar seals them in place. The laminate is then vacuum-bonded and heat cured before being removed to be trimmed and finished.
By combining shaping and fabricatio
If you want to link to this article then please use this URL: www.sail-world.com/26683