Barnacle-encrusted Mercury outboard starts after lengthy submersion
by Jonathan Revitt on 7 Jul 2014
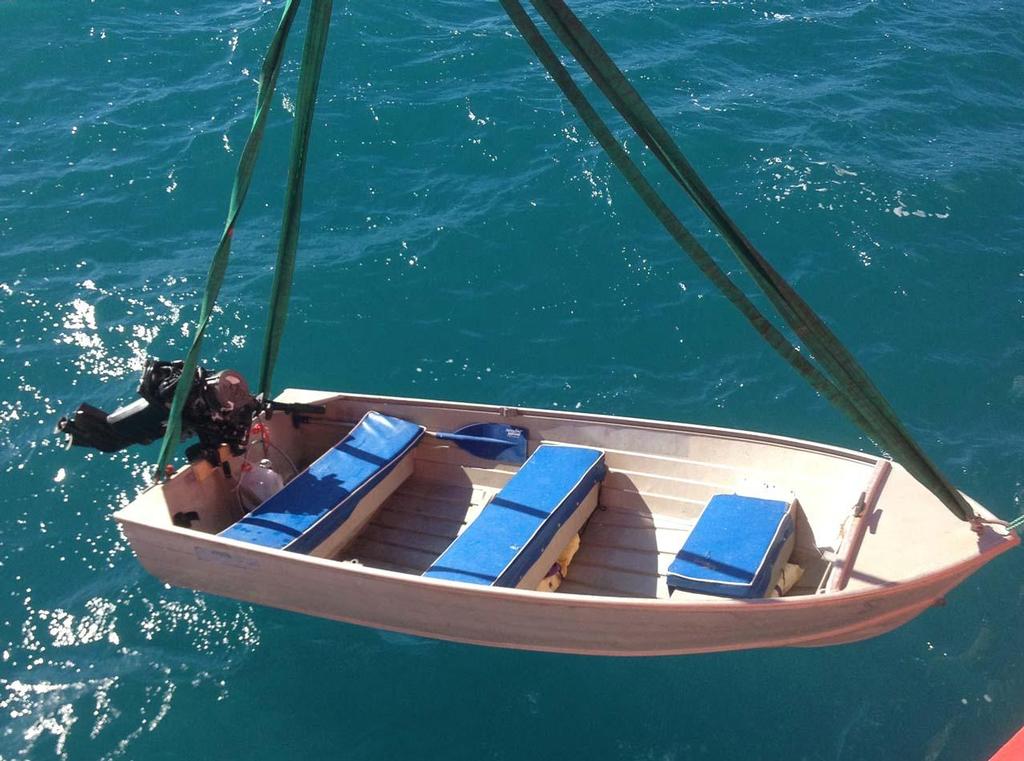
Return to Sea for Test run Mercury Marine
A barnacle-encrusted Mercury outboard recovered some 200 nautical miles off Dampier in Western Australia, started after spending months underwater.
Marine Engineer Matt Giles was working on the Offshore Support Vessel 'Far Shogun' when an upturned tinnie was spotted in the water.
'It was a 3.2m Stacer and going by the barnacles and other marine growth on the hull it looked as if it (and the engine) had been underwater for a few months at least,' he said.
Intrigued by the find, Matt and some of his mates decided to try to start the 15hp Mercury outboard.
'The crankshaft could still turn so we just cleaned the spark plugs, blew out the seawater and lubricated the cylinders,' he said. 'We drained the old fuel from the carburettor and replaced it then – to our amazement – she started.'
While the 15hp two stroke ran a little roughly at first, that soon changed.
'We removed and dismantled the carburettor and cleaned the parts in an ultrasonic bath to remove the barnacles. We then refitted it to the motor and it ran like new,' he said.
Matt and his colleagues then decided on the ultimate test and put the never-say-die motor back in the ocean.
'We had a test run of the boat on the weekend which went really well. It was a bit too windy and choppy to go more than half throttle, but it ran well. The fact that the motor started first go just blew us away,' Matt said.
Thankfully, the guys took photos and videos of the whole resurrection process.
Nicholas Webb, Mercury Marine’s Director of Outboards, Australia, New Zealand and South Pacific (ANZP) described Matt’s efforts as 'a perfect case study for Mercury’s extreme reliability'.
'An amazing resistance to sea water corrosion is built into our engines in a myriad of ways, and that’s reflected in Mercury’s 3 Year Corrosion Warranty – a warranty we offer with every recreational outboard in the range.
'We talk to customers about this every day but it’s much more powerful seeing the reality.'
Why it was possible?
Mercury's aluminium alloys – the most corrosion-resistant on the market
Aluminium alloys with less copper content are superior in resisting corrosion. Mercury's aluminium alloys contain less than .20 percent copper. The competition uses alloys with 10 to 20 times more copper content.
More stainless steel components
Stainless steel components offer maximum protection from corrosion, and Mercury outboards contain at least twice the amount of stainless steel than the competition.
Hardcoat anodizing
Mercury's superchargers, charge-air coolers and trim cylinders are hard anodized to increase corrosion resistance, wear resistance and provide better adhesion for paint.
Sacrificial anodes
Mercury strategically places sacrificial anodes on the transom brackets and lower units that are designed to sacrifice themselves and protect the aluminium alloy.
Four-step MercFusion paint system
To further protect the engine’s low-corrosion alloys, Mercury’s unique paint system delivers a further corrosion barrier by providing an excellent surface for bonding, uniform paint coverage and seal, superior flexibility and long-term adhesion, and a much harder, thicker and tougher finish.
Salt shield
Mercury's exclusive salt shield flushes into the powerhead and water passages to provide excellent resistance to saltwater exposure and heat.
Continuity devices
Mercury's stainless steel braided bonding straps complete the continuity circuit to ensure grounding for corrosion endurance.
Testing
At Mercury we engineer, build and test reliability into all of our products by thrashing them in our state-of-the-art testing centre. We always have, and we always will. Because whatever your engine type or size, consistent and reliable engine performance is an absolute must.
|
www.mercurymarine.com.au" target="_blank">Mercury Marine
If you want to link to this article then please use this URL: www.sail-world.com/124172
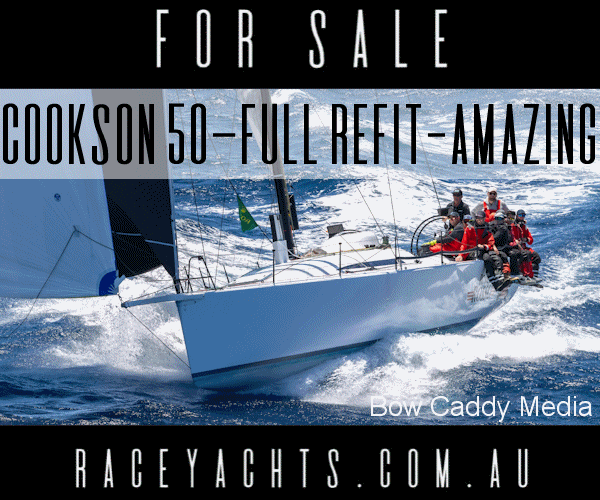
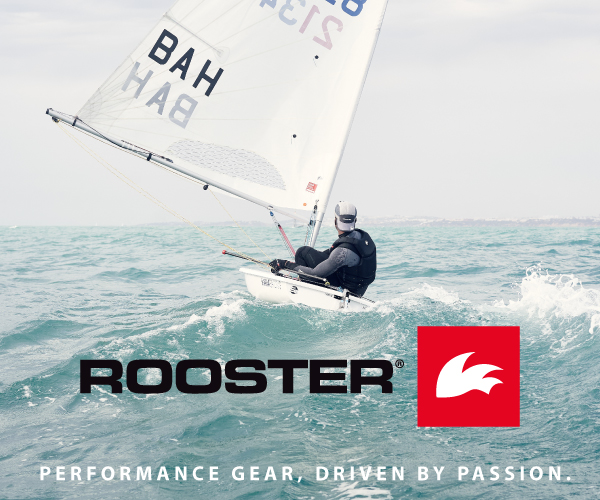