America's Cup - AC50 building program well underway at Core Builders
by Richard Gladwell, Sail-World.com on 3 Jun 2016
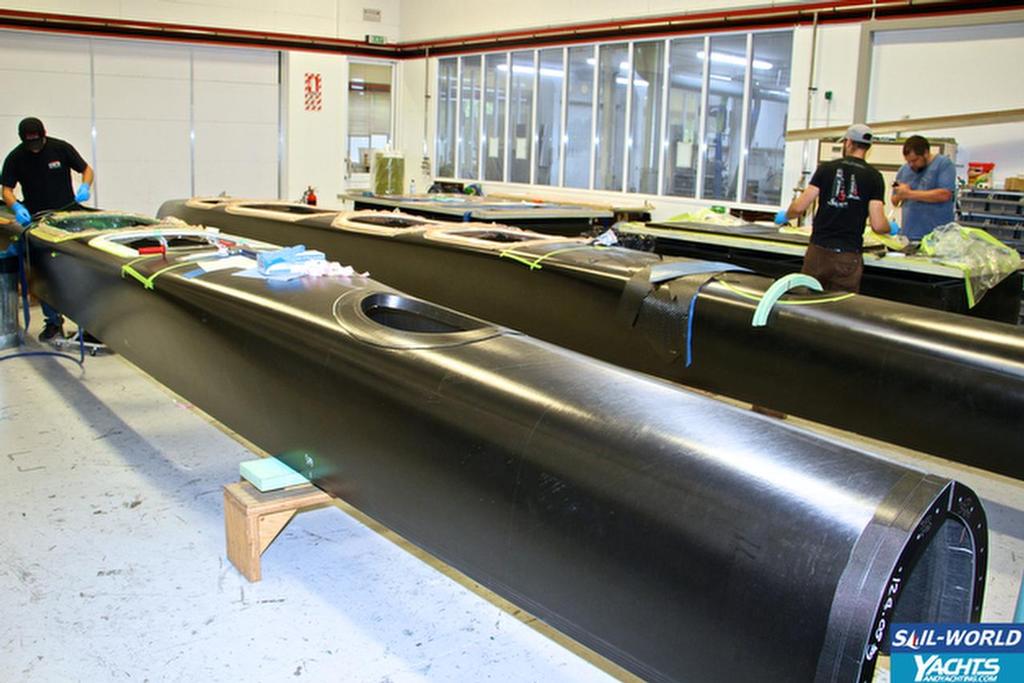
AC50 construction - Core Builders Composites - May 2016 Richard Gladwell
www.photosport.co.nz
With the forthcoming America's Cup in Bermuda just under 12 months away, production of the wingsails and AC50 one design hulls and components are well underway at Core Builders Composites in Warkworth, about an hour north of Auckland.
The facility has been used by Oracle Team USA for their America’s Cup projects dating back to the wingsailed trimaran of the 2010 America’s Cup, and again for the successful defence of the America’s Cup in 2013.
That one design America’s Cupper concept means that there is no longer any point in total secrecy during the build phase at Core Builders and for the first time in America’s Cup history, Sail-World can publish photos of America’s Cup yachts during construction.
In bygone days, building facilities tours were carefully orchestrated affairs, with media on a strict no cameras rule – if indeed, you are allowed in the facility at all. Any photos that are allowed feature some nondescript bow shot or similar – with the key people in the team posing firmly into the foreground to obscure the 'boat' as much as possible.
Not so now, as Core Builders Composites principal Tim Smyth leading Sail-World through several buildings in the Warkworth facility, while work was underway in the construction of hulls and decks, wingsails, pods and cross beams.
We were shown all the one design pieces of the AC50 platform - hulls and decks, cross beams, and pods which are identical for all teams in the 35th America's Cup. Wingsails are one-design in shape, but otherwise unrestricted.
Smyth’s only reluctance is to disclose what parts they have built for which team, as this information is protected by NDA’s and Terms of Trade. “We’ve done work for every team. We have built full Main Elements for four teams – that’s a total of eight wingsails.”
Core Builders Composites are now on their 28th wingsail build - an era which started with the 2010 America's Cup winner.
As with the AC45 One Design project leading into the San Francisco America's Cup, extensive tooling and building jig construction is required ahead of the actual build phase.
In fact, the tooling setup at Core Builders Composites is replicated in Europe.
Air freight costs for shipping large components have trebled after two airlines pulled their 747 aircraft off New Zealand routes since the last America’s Cup.
“It is actually cheaper to build down here, but the shipping cost and delivery time is the killer, and we were lucky to get any work from the European teams.”
“It made sense for there to be tooling in the Northern Hemisphere so all teams could build in a timely manner, and the European teams have all built their own hulls and decks from the common design data files.”
“In Warkworth we have built tooling for three teams in conjunction with Cookson Boats, who are building parts from that tooling for the AC50 for Emirates Team New Zealand.”
“We have built platform parts for three teams and wing parts for five teams he adds.
“Contrary to what we sometimes see from the teams, the builders all get along very well,” says Smyth. “We have collaborated effectively and efficiently to suit our timelines and produce the cheapest product,” he says.
“That includes productions of tooling, plugs, and moulds. Some parts are more efficiently produced in a part run, so we have for example produced jib tracks and platform metal parts for four teams in a single production.”
“We all know that we like the America’s Cup game and want to be in it, but we have to bring the costs down. We know that we have to avoid duplication that has no benefit.
“We are motivated. We want to see the class succeed. We want to see the Cup be healthy, and the way Teams and builders are going to make a sustainable business out of the Americas Cup is to be efficient and productive.”
Big investment in facilities
Now back up to near full strength with over 60 employees, CBC's sprawling Warkworth complex resembles more an aircraft factory than a boat building facility. Three CNC large format composite milling machines are now on site, the largest (18m x 6m x 3m) located in what used to be the multi-story print hall of the printing and publishing company that previously occupied the premises.
The two others sit side by side and are capable of working on a component of a maximum dimension of 6.0m x 2.6m and 1.2 metres.
“With a more compressed dagger board construction time and more orders, the bottleneck is often the CNC machine, so it made sense to get another machine on site,” explains Smyth.
Core Builders will construct the daggerboards and rudders for Oracle Team USA and Softbank Team Japan, but no-one else. “The timelines are to tight and the designs for these are proprietary so need careful management” says Smyth.
The AC50 project is an extension of what was done in the build-up to the last America’s Cup where a fleet of AC45 One Design wingsailed catamaran was produced. Now converted to be AC72 style foilers those same boats are now used in their second America’s Cup World Series.
For the AC50 project, many of the same techniques are employed to produce everything from hulls to cross beams and wingsails for the foiling catamarans.
The fact that the basic boat platform parts are all one-design has meant that they must be produced to excruciatingly tight tolerances, and the assembly process gets equal attention with the building process to ensure that the boat’s one design components are as close to being a one-design as possible.
The AC50s hulls are constructed in female moulds split into two halves with an upper and a lower section - the deck complete with cockpit cut-outs in which the helmsman and grinders will work, and the lower half of the hull which carries most of the structure including cockpit floor.
“Last time we split the AC72 on a vertical line, this time with the AC50, we are splitting the hulls on a horizontal line,' Smyth explains.
' Having a separate transom last time for the AC45 proved to be quite labour intensive. Without the bow it made sense to split the hull horizontally to get a comfortable assembly process.
'It makes the assembly much easier. Obviously, the aim is to fit into a 40ft container, which is why the bow comes off in the first place.'
Two-part hull construction process
Once built the hull parts are released from the female tooling they are moved to a CNC cut assembly jig where both parts are carefully anchored to maintain their moulded shapes. It’s a fact of life that curing epoxy resin shrinks and composite parts distort slightly after cure so they do not necessarily maintain their design shape to the tolerances required by the rule.
With the AC50, the whole construction process is so intertwined that unless it all fits together perfectly then the boat won’t measure. Smyth points out that a plug can be measured, as can a mould taken from that plug, as can the piece of the boat that comes out of the mould, but the only thing that really matters is whether the final hull actually measures to be within the tolerances of the Class Rule.
With the lower part of the hull in place, the deck sections are offered down onto it, and the monocoque formed by the now bonded bottom and upper hull pieces should measure precisely to the designed shape from the original AC50 designers – thus completing the loop between the whole design, construction and finished boat.
All the AC50 builders cut their tooling using CNC processes from data files produced from the class designers’ CAD files. The process combined with facilities such as those at Core Builders Composites means that the original design is produced to tolerances of less than a millimetre.
While the external shape is identical, teams are allowed to strengthen the boat in various places to cope with the loadings of the foils and rigs their design teams have devised, however, they are not permitted to reduce the structural strength below the designed minimum.
Although there is provision for individual measurement to within a couple of millimetres of tolerance, Smyth says the measurers have accepted the one design mould and the integrity of the building process to simplify the measurement process.
“That point is lost on many people,” says Smyth. “If we had too rigid a measurement protocol the measurers would be disappearing up their own backsides trying to accurately check the boats. The whole world is seduced by paying to avoid risk and capture perceived transgressions.
'It is just money down the drain. But the threats are couched in terms of being flicked from the America’s Cup, and your $100 million campaign will be for nothing if you are 2mm mm too fat or skinny in a part of the boat.
“Of course, it makes no speed difference at all and even the process of checking it with absolute certainty is a not at all straightfoward.”
Core Builders Composites have also invested in cost reduction methods and materials for manufacturing composite tooling. “We are using cheaper mould making techniques and cheaper carbon fibre, including a lot of recycled carbon fibre to build all carbon moulds. We prefer to use all carbon moulds because they stay nice and true,” Smyth explains.
Even with Emirates Team NZ having their boat built by another builder the same one design process has been followed. “We worked with Cookson Boats to produce the tools for both ourselves and Team New Zealand. We both collaborated to find the most cost-effective way to build while still meeting our desired timelines.'
Part 2 will follow in a day or so on www.sail-world.com
If you want to link to this article then please use this URL: www.sail-world.com/145233